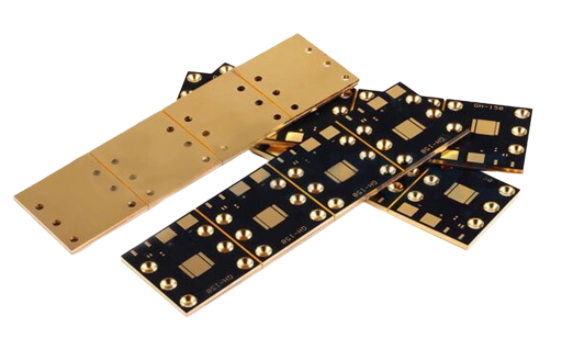
MCPCB Full Form and Basic Structure
MCPCB stands for Metal Core Printed Circuit Board. The fundamental structure consists of three layers: a metal base layer (aluminum or copper), a thermally conductive dielectric layer, and a copper circuit layer where components are mounted.
The metal core serves as a heat spreader, transferring thermal energy 8 to 9 times faster than traditional FR4 PCBs. This efficient heat transfer keeps temperature-sensitive components within optimal operating ranges, significantly improving performance and extending component lifespan.
MCPCB Material Options
Aluminum Core PCBs represent the most common type due to their optimal balance of thermal performance, weight, and cost. Aluminum offers excellent thermal conductivity while remaining lightweight and cost-effective for most applications.
Copper Core PCBs provide superior thermal performance for high-power applications requiring maximum heat dissipation. Though more expensive than aluminum, copper delivers exceptional thermal conductivity for demanding thermal management scenarios.
Steel Core PCBs offer enhanced mechanical strength for industrial environments, though they are less common due to manufacturing challenges and lower thermal performance compared to aluminum and copper options.
Metal Core PCB Thickness and Specifications
Standard metal core PCB thickness ranges from 30 mil to 125 mil (0.76mm to 3.18mm), with custom thicknesses available for specific applications. The metal substrate typically comprises the majority of the total board thickness.
MCPCB copper foil thickness ranges from 1 oz to 10 oz, with heavier copper weights supporting higher current applications and improved thermal distribution. The dielectric layer thickness varies based on voltage requirements and thermal performance specifications.
These specifications directly impact thermal resistance and heat transfer efficiency, making proper thickness selection critical for optimal performance.
Welcome to read: Detailed explanation of metal-based PCB manufacturing process
Metal Core PCB LED Applications
LED technology represents the primary application for MCPCBs due to the significant heat generation of high-power LEDs. Metal core PCBs enable LED systems to operate at higher power densities while maintaining proper thermal management.
Common LED applications include automotive lighting, street lighting, architectural illumination, display backlighting, and general lighting systems. The superior heat dissipation reduces the number of LEDs required for specific illumination levels while extending operational life.
Additional applications include solar panels, motion control systems, power converters, and any electronics requiring effective thermal management for high-power components.
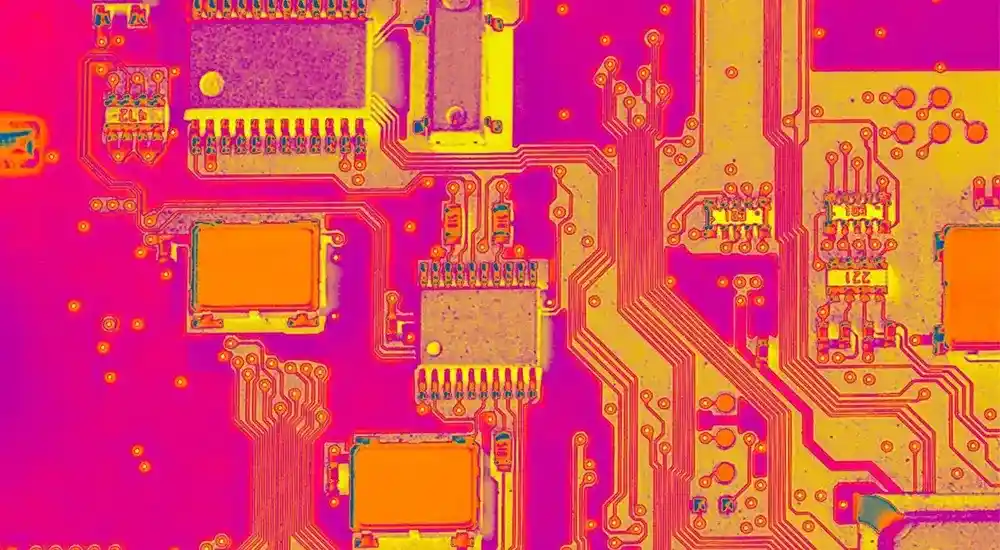
Advantages of Metal Core PCBs
Superior Thermal Management represents the primary advantage of MCPCBs, with heat transfer rates 8 to 9 times faster than traditional FR4 boards. This exceptional thermal conductivity enables efficient heat dissipation from high-power components, maintaining optimal operating temperatures and preventing thermal damage.
Enhanced Power Density capabilities allow designers to implement higher power components in more compact configurations. The effective thermal management supports increased current loads and power levels without compromising performance or reliability standards.
Improved Electrical Performance results directly from better thermal control. Components operating at lower temperatures exhibit enhanced efficiency, reduced electrical resistance, and more stable performance characteristics. LED applications particularly benefit from improved luminous efficacy and color stability.
Extended Component Lifespan emerges from reduced thermal stress on electronic components and solder joints. Lower operating temperatures significantly decrease failure rates and extend the operational life of critical components, particularly beneficial for LED chips and power semiconductors.
Better Dimensional Stability compared to traditional PCBs ensures reliable performance across temperature variations. Metal cores provide superior mechanical strength and reduced thermal expansion coefficients, maintaining structural integrity under thermal cycling conditions.
Reduced System Complexity through elimination of additional cooling hardware such as heat sinks, thermal interface materials, and cooling fans. This simplification reduces both material costs and assembly complexity while improving overall system reliability and reducing potential failure points.
Haoyue Electronics: Professional MCPCB Manufacturer
Selecting an experienced MCPCB manufacturer ensures optimal thermal performance and product reliability. Haoyue Electronics specializes in metal core PCB manufacturing and assembly, providing comprehensive solutions for demanding thermal management applications.
Our manufacturing capabilities include aluminum core, copper core, and custom metal substrate options engineered for diverse performance requirements. We maintain strict quality control standards throughout production to ensure consistent thermal performance and electrical reliability.
Haoyue Electronics offers complete PCB assembly services for integrated MCPCB solutions, combining manufacturing expertise with comprehensive technical support. Our engineering team assists with design optimization and specification selection to achieve maximum performance and cost effectiveness for your specific application requirements.
Related Articles
- For a deeper look at how aluminum and copper cores affect heat transfer, check out our guide:
Metal Core PCB Thermal Conductivity - Want practical tips on improving PCB heat dissipation? Explore our article on
Metal Core PCB Thermal Management
From prototype to production — we help hardware teams cut costs, improve yields, and scale faster. Let’s make your next product a success!