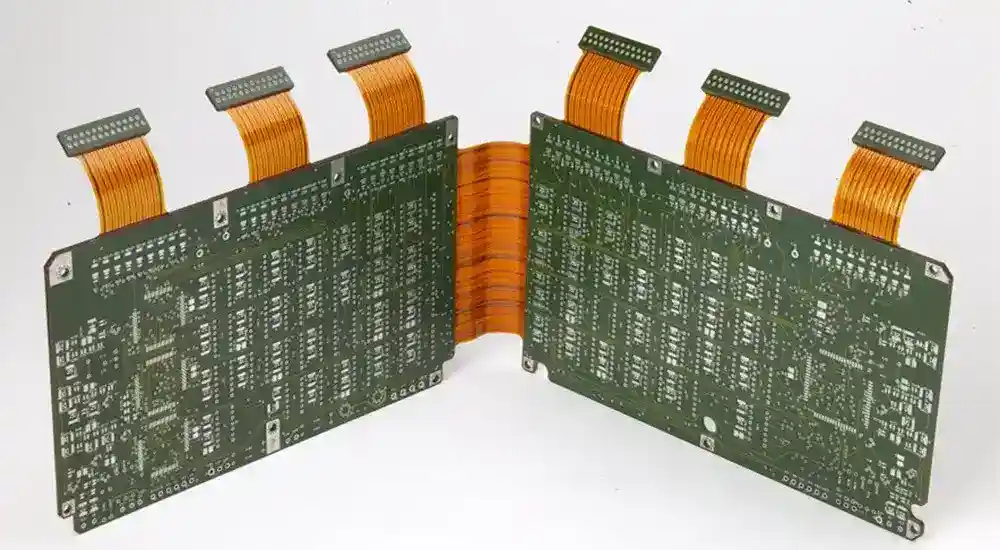
Introduction
Flexible PCBshave revolutionized modern electronics manufacturing by enabling unprecedented design capabilities in compact spaces. As electronic devices continue to shrink while demanding greater functionality, flexible printed circuit boards have emerged as the critical enabler of next-generation electronic innovations.
The global flexible PCB market, valued at approximately $15.2 billion in 2023, is projected to reach $61.75 billion by 2032, driven by increasing demand for miniaturized electronics, automotive electrification, and advanced medical devices.
What Is a Flexible PCB?
A flexible PCB is a printed circuit board manufactured using flexible substrate materials that allow the board to bend, fold, and flex without compromising electrical performance. The fundamental distinction lies in substrate construction: while rigid PCBs utilize fiberglass-reinforced materials like FR4, flex circuit boards employ specialized polymer films that maintain electrical connectivity under mechanical stress.
This enables electronic designers to create innovative form factors and utilize three-dimensional spaces previously impossible with conventional rigid boards.
Structure and Key Components
1. Layer Architecture
The structural foundation consists of multiple precisely engineered layers: a polyimide (PI) substrate providing exceptional thermal stability and mechanical durability, conductive copper foil layers creating electrical pathways with thicknesses ranging from 0.5 to 2 ounces per square foot, and protective coverlay films shielding copper traces while maintaining flexibility. Modern manufacturing offers both rolled annealed (RA) and electrodeposited (ED) copper options, each providing specific advantages for different applications.
2. Configuration Types
Single-Layer Flexible PCBs
Feature copper traces on one side of the substrate, offering highest flexibility for applications requiring frequent bending or tight bend radius requirements.
Double-Layer Flexible PCBs
Incorporate copper traces on both sides connected through plated through-holes, representing 44.3% of the global market share as the most popular choice for moderately complex circuits.
Multi-Layer Flexible PCBs
Advanced applications require multiple conductive layers separated by insulating materials, typically using 4–8 layers for optimal performance while maintaining flexibility.
3. Reinforcement Components
Stiffener Sections
Rigid reinforcement areas provide mechanical stability for component mounting and connector attachment, typically fabricated from FR4 material, polyimide film, or thin metal sheets.
Connector Interfaces
Specialized connector designs accommodate flexible substrate properties and often incorporate strain relief features to prevent damage during repeated connection cycles.
Materials Used in Flexible PCB Manufacturing Processes
1. Substrate Materials
Polyimide Films
The gold standard for flexible PCB substrates, polyimide offers exceptional thermal stability, chemical resistance, and mechanical properties. Leading manufacturers including DuPont (Kapton), Kaneka (Apical), and Taimide produce specialized films with dielectric constants ranging from 2.78 to 3.48 at 1Hz and low dielectric loss between 0.01 and 0.03, ensuring reliable signal transmission in high-frequency applications.
Polyester (PET) Films
Cost-effective alternative for applications with less demanding thermal and chemical requirements, providing adequate performance for consumer electronics where cost optimization is critical.
PTFE (Polytetrafluoroethylene)
Specialized applications requiring ultra-low dielectric constant and exceptional chemical resistance utilize PTFE substrates, excelling in aerospace and high-frequency communication applications.
2. Conductive Materials
Copper Foil Types
Modern manufacturing employs rolled annealed copper for superior flexibility and fatigue resistance in dynamic flexing applications, while electrodeposited copper offers better adhesion and uniformity for static bend applications. Copper thickness selection directly impacts both electrical performance and mechanical flexibility.
3. Adhesive Systems
Conventional flexible PCBs utilize acrylic adhesives to bond copper foil to polyimide substrates, while advanced adhesiveless laminates eliminate adhesive layers through specialized chemical and thermal processes. Adhesiveless construction improves thermal performance, reduces thickness, and enhances electrical properties, though at increased manufacturing cost, making it ideal for high-performance applications.
4. Coverlay Materials
Standard coverlay films consist of polyimide base material with acrylic adhesive backing, providing excellent protection while maintaining flexibility. Applications requiring enhanced chemical resistance may utilize specialized coatings including liquid photoimageable coverlays or solder mask materials designed for flexible substrates.
Manufacturing Overview
1. Process Flow
Flexible PCB manufacturing begins with substrate preparation where polyimide films are cleaned and prepared for copper lamination. Copper foil is bonded using either adhesive or adhesiveless lamination processes, followed by photolithographic circuit patterning using specialized photoresists. The etching process removes unwanted copper while preserving designed circuit traces, and via formation provides interconnection between layers through precise laser drilling and plating processes.
2. Forming Operations
Precision cutting operations create the final board outline and features through laser cutting for superior accuracy and minimal substrate damage, or die cutting for cost-effective high-volume production. Both methods require careful process control to prevent delamination or stress concentrations that could compromise long-term reliability.
3. Quality Control
Manufacturing quality control incorporates specialized testing procedures including bend testing, thermal cycling, and electrical continuity verification to ensure flexible PCBs meet performance specifications throughout their operational lifecycle.
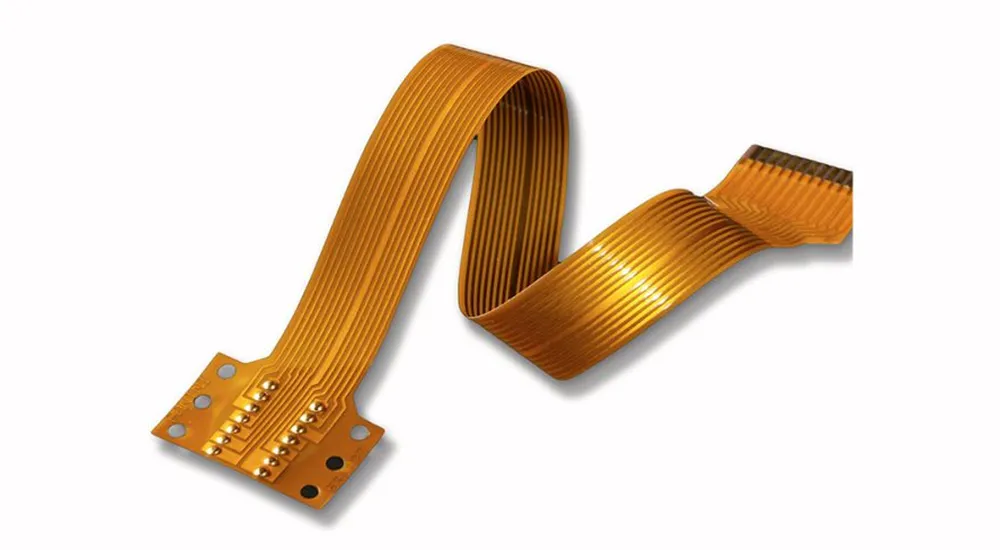
Key Advantages of Flexible PCBs
1. Mechanical Benefits
Unprecedented Flexibility
Modern flexible PCBs can withstand millions of flex cycles while maintaining electrical integrity, enabling three-dimensional design freedom that allows electronic designers to utilize available space efficiently by conforming to product enclosures. This capability supports dynamic flexing applications such as robotic systems or wearable devices requiring continuous movement.
2. Space and Weight Optimization
Miniaturization Support
Flexible PCBs eliminate the need for connectors and cable assemblies, reducing overall system size and weight—critical in aerospace, medical, and portable electronics applications. By replacing multiple rigid boards and interconnection systems with single flexible circuits, manufacturers can simplify assembly processes and improve reliability.
3. Reliability Enhancements
The flexible nature provides inherent vibration dampening, reducing stress on solder joints and components, particularly valuable in automotive and industrial applications. Additionally, flexible PCBs can distribute heat more effectively than rigid boards by utilizing available three-dimensional space for thermal dissipation, while eliminating mechanical connectors removes a common failure point and improves overall system reliability.
Limitations and Design Considerations
1. Cost Factors
Flexible PCBs typically cost 2–5 times more than equivalent rigid PCBs due to specialized materials, manufacturing processes, and lower production volumes. The cost differential is most significant for simple circuits but becomes more reasonable for complex, high-density designs.
2. Mechanical Constraints
Bend Radius Requirements
Each design must respect minimum bend radius specifications to prevent copper trace cracking or delamination. Tighter bend radii require thinner copper and specialized design rules.
Limited Thickness Range
Flexible PCBs are constrained to relatively thin constructions, typically ranging from 0.008 to 0.24 inches total thickness, which can restrict component selection and current-carrying capacity.
3. Handling and Assembly Challenges
Delicate Construction
Flexible PCBs require careful handling during assembly to prevent damage from excessive bending or sharp edges. The flexible nature can complicate component mounting processes, particularly for larger components that may require additional mechanical support.
4. Repair and Rework Difficulties
The thin, flexible construction makes field repairs extremely challenging. Damaged flexible PCBs often require complete replacement rather than repair, increasing long-term maintenance costs.
Applications Across Industries
1. Consumer Electronics
The consumer electronics sector represents the largest market for flexible PCBs, accounting for 51.3% of global demand in 2023. Smartphones utilize flexible circuits for camera modules, display connections, and internal interconnections enabling ultra-thin designs.
Wearable Technology
Smartwatches, fitness trackers, and health monitoring devices rely on flexible PCBs to conform to curved surfaces and withstand continuous movement, essential for user comfort and device durability.
Foldable Displays
Emerging foldable smartphone and tablet technologies depend entirely on flexible PCB technology to enable hinge mechanisms and display connections that can withstand thousands of folding cycles.
2. Automotive Electronics
The automotive industry embraces flexible PCB technology for its ability to withstand harsh environmental conditions including temperature extremes, vibration, and chemical exposure.
Advanced Driver Assistance Systems (ADAS)
Modern vehicles incorporate numerous sensors and cameras requiring flexible connections to accommodate vehicle movement and vibration, providing necessary durability and reliability for safety-critical applications.
LED Lighting Systems
Automotive LED headlights and interior lighting systems utilize flexible PCBs to create compact, efficient lighting solutions that conform to vehicle design requirements while withstanding thermal cycling and vibration.
Infotainment and Dashboard Systems
Curved displays and control interfaces require flexible PCBs to connect various components while maintaining aesthetic appeal and functional reliability.
3. Medical Device Applications
The medical device industry demands the highest levels of reliability and biocompatibility, making flexible PCBs ideal for implantable devices and diagnostic equipment.
Implantable Devices
Pacemakers, defibrillators, and neurostimulators utilize flexible PCBs to create compact, reliable connections that withstand the challenging environment inside the human body while conforming to anatomical structures.
Diagnostic Equipment
Medical imaging systems including MRI and CT scanners incorporate flexible PCBs to connect sensors and components in confined spaces while maintaining signal integrity.
Wearable Medical Devices
Continuous monitoring devices such as glucose monitors and cardiac monitors rely on flexible PCBs to provide comfortable, reliable connections that withstand daily wear and movement.
4. Aerospace and Industrial
Satellite Communications
Extreme space environmental conditions require electronic systems that can withstand radiation, temperature cycling, and mechanical stress. Flexible PCBs provide necessary reliability and performance for satellite communication systems and scientific instruments.
Industrial Automation
Robotic systems and automated manufacturing equipment utilize flexible PCBs to create reliable connections in moving assemblies, essential for maintaining production efficiency.
Aerospace Avionics
Commercial and military aircraft incorporate flexible PCBs in navigation, communication, and control systems where reliability and weight reduction are critical requirements.
Future Outlook and Technological Trends
1. Market Growth Projections
The flexible PCB market is experiencing unprecedented growth, with projections indicating expansion from $15.2 billion in 2023 to $61.75 billion by 2032. Multi-layer flexible PCBs represent the fastest-growing segment, with expected compound annual growth rates exceeding 15% through 2032, reflecting increasing complexity of electronic systems and need for high-density interconnections in compact form factors.
2. Emerging Technologies
Stretchable Electronics
Next-generation flexible PCBs will incorporate stretchable materials that can elongate in multiple directions while maintaining electrical connectivity, enabling new applications in wearable electronics and biomedical devices.
Advanced Materials
Research into graphene-enhanced substrates and conductive polymers promises to deliver flexible PCBs with superior electrical performance and mechanical properties.
5G and High-Frequency Applications
The deployment of 5G networks requires flexible PCBs capable of handling higher frequencies while maintaining signal integrity in compact, curved form factors.
3. Manufacturing Innovation
Automated Production
Advanced manufacturing automation is reducing flexible PCB production costs while improving quality consistency. Roll-to-roll processing and automated inspection systems are becoming standard in high-volume production facilities.
3D Printing Integration
Additive manufacturing techniques are being integrated with traditional flexible PCB production to create hybrid structures with enhanced three-dimensional capabilities.
Partner with Haoyue Electronics for Advanced Flexible PCB Solutions
At Haoyue Electronics, we combine over a decade of specialized expertise in flexible PCB manufacturing with cutting-edge technology to deliver solutions that meet the most demanding applications. Our comprehensive capabilities span from prototype development through high-volume production, ensuring your flexible PCB projects achieve optimal performance and reliability.
Our advanced manufacturing facilities utilize the latest adhesiveless lamination processes, precision laser cutting systems, and automated quality control technologies to produce flexible PCBs that exceed industry standards. We work with leading material suppliers to offer the complete range of polyimide substrates, specialized copper foils, and protective coverlays necessary for your specific application requirements.
Whether you’re developing next-generation wearable devices, automotive electronics, or critical medical equipment, our engineering team provides comprehensive design support to optimize your flexible PCB solution for performance, reliability, and cost-effectiveness. We understand the unique challenges of flexible PCB design and manufacturing, and we’re committed to helping you transform innovative concepts into successful products.
Contact Haoyue Electronics today to discuss how our flexible PCB expertise can support your next project. Our team is ready to provide detailed technical consultation, competitive quotations, and rapid prototype development to accelerate your time-to-market while ensuring exceptional quality and reliability.