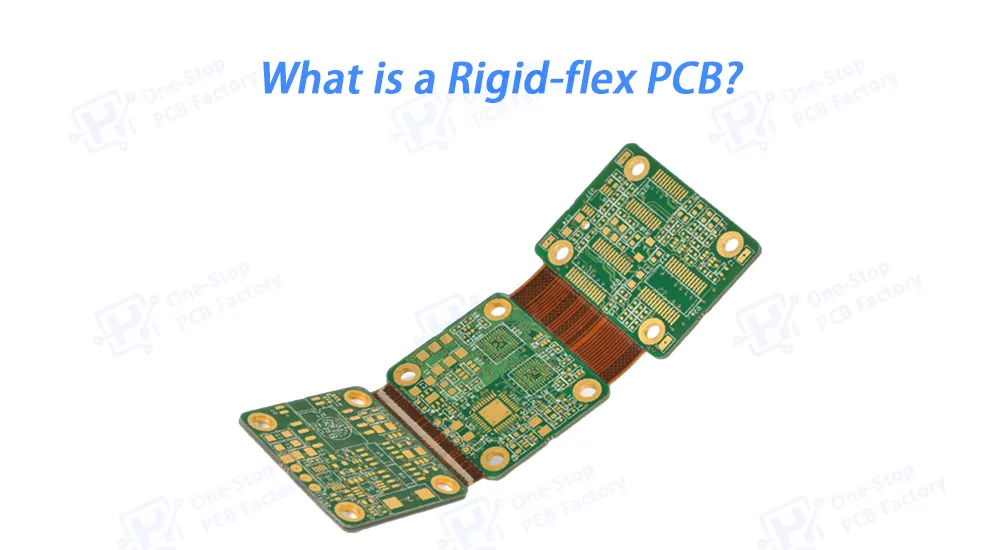
Understanding Rigid-Flex PCB Fundamentals
Definition and Core Structure
A rigid-flex PCB is an advanced circuit board technology that integrates rigid and flexible substrate materials within a single interconnected assembly. This hybrid construction eliminates traditional connectors and cables by creating seamless electrical pathways between rigid component mounting areas and flexible interconnection zones.
The basic structure consists of multiple layers where flexible polyimide substrates are strategically bonded with rigid materials such as FR4 at designated locations. The flexible sections utilize thin copper conductors laminated between polyimide films, while rigid areas provide mechanical stability and standard component mounting surfaces.
Essential Characteristics
Rigid-flex PCBs deliver several critical advantages that distinguish them from conventional PCB solutions:
- Enhanced Signal Integrity: Elimination of connectors reduces impedance discontinuities and signal degradation
- Improved Reliability: Fewer solder joints and mechanical connections minimize potential failure points
- Three-Dimensional Design Freedom: Enables complex folding configurations impossible with rigid boards alone
- Space Optimization: Compact packaging solutions ideal for miniaturized electronic systems
- Reduced Assembly Complexity: Single-piece construction eliminates cable management and connector assembly
Material Composition and Properties
The performance characteristics of rigid-flex PCBs depend heavily on material selection and layer construction:
Material Component | Primary Function | Key Properties |
---|---|---|
Polyimide Film | Flexible substrate | High temperature resistance, excellent flexibility |
Copper Foil | Conductor layers | Various weights (0.5-2 oz), controlled thickness |
Adhesive Systems | Layer bonding | Acrylic or polyimide-based, temperature-dependent |
Rigid Substrates | Component mounting | FR4, high-Tg materials, dimensional stability |
Coverlay Materials | Protection | Polyimide or solder mask, environmental protection |
Design Principles and Technical Considerations
Mechanical Design Requirements
Successful rigid-flex PCB implementation requires careful attention to mechanical design parameters that ensure long-term reliability under operational stress conditions.
Bend Radius Specifications
The minimum bend radius represents a critical design parameter that prevents conductor fracture and substrate failure:
- Static Applications: Minimum 6-10 times total flexible section thickness
- Dynamic Applications: Minimum 10-20 times thickness for repeated flexing
- High-Reliability Systems: Conservative ratios of 20-25 times thickness recommended
- Material Considerations: Thinner copper weights enable tighter bend radii
Transition Zone Design
The interface between rigid and flexible sections requires specialized design approaches to manage stress concentration:
- Gradual Thickness Transitions: Stepped layer terminations prevent abrupt stress changes
- Strain Relief Features: Curved routing and generous spacing reduce mechanical stress
- Anchor Point Design: Secure attachment methods prevent delamination under flexing
- Support Material Placement: Strategic use of stiffeners where mechanical support is needed
Electrical Design Optimization
Electrical performance optimization in rigid-flex PCBs involves multiple design considerations that affect signal integrity and manufacturing yield.
Layer Stack-up Configuration
Layer Count | Typical Application | Design Considerations |
---|---|---|
2-4 Layers | Simple interconnects | Basic routing, cost-effective |
4-8 Layers | Mixed-signal systems | Controlled impedance, power distribution |
8-16 Layers | High-speed digital | Advanced signal integrity, EMI control |
16+ Layers | Complex systems | Specialized manufacturing, thermal management |
Signal Routing Guidelines
Optimal electrical performance requires adherence to specific routing practices:
- Conductor Placement: Position traces in neutral bending planes to minimize stress
- Via Design: Use microvias and controlled-depth drilling for layer transitions
- Impedance Control: Maintain consistent dielectric thickness and conductor geometry
- Ground Plane Management: Provide continuous reference planes for high-speed signals
Applications and Industry Implementation
Aerospace and Defense Applications
The aerospace and defense industries represent primary markets for rigid-flex PCB technology due to stringent reliability requirements and space constraints.
Military and Avionics Systems
Critical applications in this sector leverage the technology’s inherent advantages:
- Radar Systems: Complex antenna arrays requiring precise signal routing and mechanical flexibility
- Satellite Technology: Weight-sensitive applications where connector elimination provides significant benefits
- Avionics Equipment: Cockpit displays and control systems requiring high reliability under vibration
- Communication Systems: Portable military radios and tactical communication equipment
Performance Requirements
Application Area | Key Requirements | Rigid-Flex Advantages |
---|---|---|
Space Systems | Weight reduction, reliability | Connector elimination, compact design |
Military Electronics | Shock/vibration resistance | Mechanical integrity, fewer failure points |
Avionics | Signal integrity, EMI control | Controlled impedance, shielding capability |
Medical Device Applications
Medical device manufacturers increasingly adopt rigid-flex PCBs for applications requiring biocompatibility, miniaturization, and exceptional reliability.
Implantable and Portable Devices
The medical sector utilizes rigid-flex technology across diverse applications:
- Implantable Systems: Pacemakers, neural stimulators, and drug delivery devices
- Diagnostic Equipment: Portable ultrasound systems, blood glucose monitors, and vital sign monitors
- Surgical Instruments: Minimally invasive surgical tools and endoscopic equipment
- Hearing Aids: Ultra-compact form factors with complex three-dimensional routing requirements
Consumer Electronics Integration
Consumer electronics drive significant innovation in rigid-flex PCB technology through demands for thinner profiles and enhanced functionality.
Mobile and Wearable Technology
Modern consumer devices extensively implement rigid-flex solutions:
- Smartphones: Camera modules, display connections, and antenna systems
- Tablets: Hinge mechanisms and display interconnections
- Wearable Devices: Fitness trackers, smartwatches, and health monitoring systems
- Gaming Systems: Portable gaming devices and controller assemblies
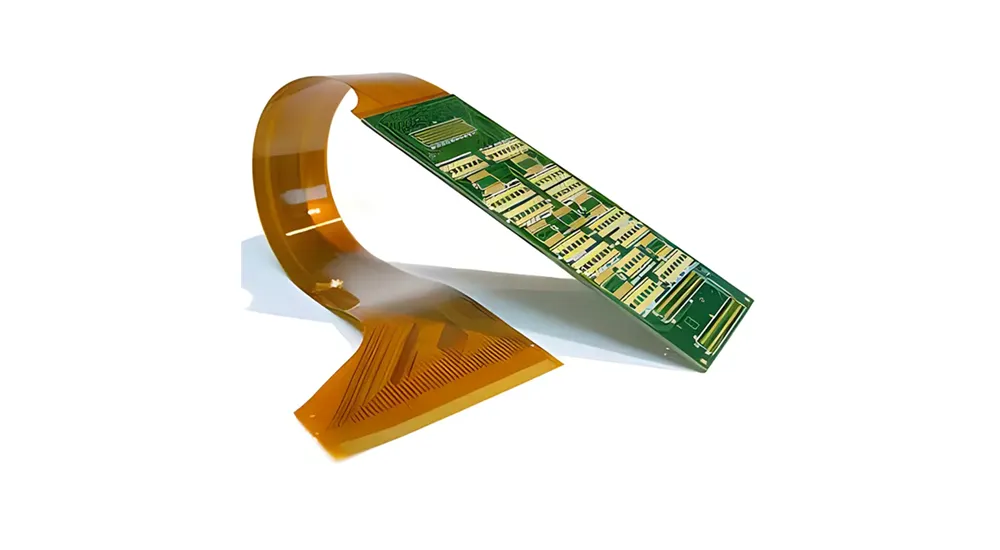
Manufacturing Excellence and Haoyue Electronics Capabilities
Advanced Manufacturing Processes
Modern rigid-flex PCB manufacturing requires sophisticated equipment and precise process control to achieve consistent quality and reliability.
Production Technology Requirements
State-of-the-art manufacturing facilities must incorporate specialized capabilities:
- Controlled Lamination Systems: Precise temperature and pressure control for multi-material bonding
- Precision Drilling Technology: Laser and mechanical drilling systems for various substrate materials
- Advanced Imaging Systems: High-resolution inspection equipment for complex geometries
- Specialized Testing Equipment: Mechanical stress testing and electrical performance validation
Quality Control Standards
Process Stage | Critical Parameters | Inspection Methods |
---|---|---|
Material Preparation | Moisture control, thickness uniformity | Automated measurement systems |
Lamination | Temperature profiles, pressure distribution | Real-time process monitoring |
Drilling/Routing | Positional accuracy, edge quality | Optical inspection, measurement |
Final Testing | Electrical continuity, mechanical integrity | Automated test equipment |
Haoyue Electronics Manufacturing Capabilities
Haoyue Electronics has established comprehensive rigid-flex PCB manufacturing capabilities that address demanding applications across multiple industries. Our state-of-the-art facility incorporates advanced lamination systems, precision drilling equipment, and automated optical inspection technology to ensure consistent quality standards.
Technical Specifications and Services
Our manufacturing capabilities encompass the full spectrum of rigid-flex PCB requirements:
- Layer Count Range: From simple 2-layer constructions to complex 20+ layer assemblies
- Material Options: Various polyimide films, adhesive systems, and specialized substrates
- Precision Capabilities: Minimum trace widths of 75 micrometers with controlled impedance routing
- Quality Standards: IPC Class 3 manufacturing with comprehensive testing protocols
Engineering Support Services
Haoyue Electronics provides comprehensive design support services that optimize both performance and manufacturability:
- Design Rule Verification: Early validation of design parameters against manufacturing capabilities
- Stack-up Optimization: Material selection and layer arrangement for optimal performance
- Cost Engineering: Design for manufacturability consulting to optimize production efficiency
- Reliability Analysis: Mechanical stress modeling and thermal cycle testing validation
Our engineering team collaborates closely with customers throughout the development process, from initial concept through production ramp-up. This partnership approach ensures that rigid-flex PCB designs meet both technical requirements and manufacturing feasibility constraints while maintaining cost-effectiveness.
Conclusion
Rigid-flex PCB technology represents a sophisticated solution for modern electronic systems requiring compact packaging, enhanced reliability, and superior electrical performance. The successful implementation of these advanced circuit boards requires careful consideration of mechanical design principles, electrical optimization techniques, and manufacturing capabilities.
The technology continues to evolve with advancing materials science and manufacturing processes, enabling increasingly complex applications across aerospace, medical, and consumer electronics markets. As electronic systems become more sophisticated and miniaturized, rigid-flex PCBs will play an increasingly critical role in enabling next-generation product development.
Haoyue Electronics specializes in advanced rigid-flex PCB manufacturing with comprehensive engineering support and quality assurance capabilities. Our experienced team delivers reliable solutions for critical applications across aerospace, medical, and industrial markets. Contact our engineering specialists to discuss your rigid-flex PCB requirements and discover how our manufacturing excellence can support your next innovative project.