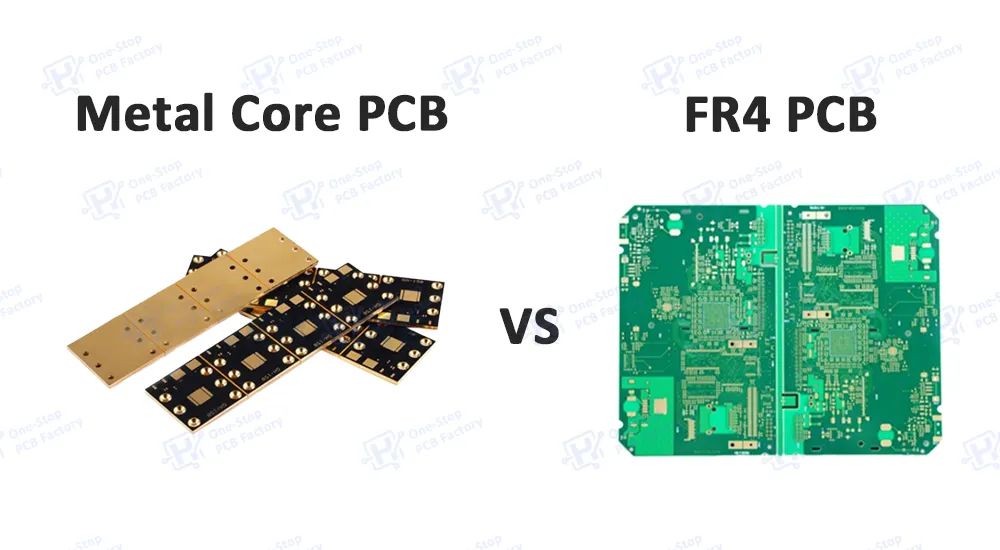
This comprehensive guide examines the key differences between metal core PCBs (MCPCBs) and FR4 PCBs, providing technical insights to help you make informed decisions for your next project.
Metal Core PCB vs FR4 PCB: Technical Comparison
1. Thermal Performance Analysis
The most significant difference lies in thermal management capabilities:
Heat Dissipation Efficiency
- Traditional FR4 PCBs exhibit thermal resistance approximately 32% higher than aluminum PCBs
- Metal core PCBs achieve thermal conductivity 20-30x higher than standard FR4
- MCPCBs eliminate the need for secondary heat sinks in many applications
Temperature Limits
- MCPCBs can withstand temperatures up to 400°C
- Standard FR4 limited to 130-140°C, high-Tg variants to 170°C
2. Manufacturing and Cost Considerations
The most significant difference lies in thermal management capabilities:
Production Complexity
- FR4: Standard processes, high-volume capability, shorter lead times
- MCPCB: Specialized equipment required, longer lead times, higher setup costs
Material Costs
- FR4: $0.20-0.80 per square inch
- MCPCB: $2-8 per square inch (3-10x higher initial cost)
3. Application-Specific Performance
High-Power LED Applications
MCPCBs in LED applications ensure lowest possible operating temperature and maximum brightness, with single-layer designs providing mechanical strength and thermal efficiency.
High-Frequency Applications
FR4’s dielectric constant variations can cause signal integrity issues in high-frequency designs, while MCPCBs may introduce different challenges due to metal substrate effects.
Advantages and Disadvantages: Side-by-Side Comparison
Metal Core PCB
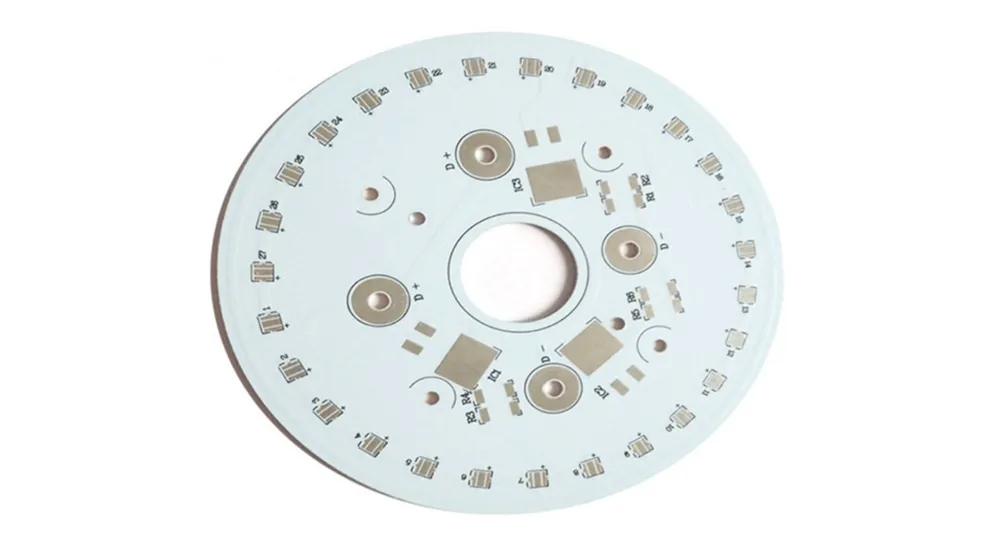
Advantages | Disadvantages |
---|---|
Excellent heat dissipation (1-9 W/mK thermal conductivity) | Higher material costs (3-10x FR4) |
Superior mechanical strength and durability | Limited layer count options |
Built-in EMI shielding | Specialized manufacturing requirements |
Reduced reliance on heat sinks and cooling hardware | Heavier than FR4 substrates |
FR4 PCB
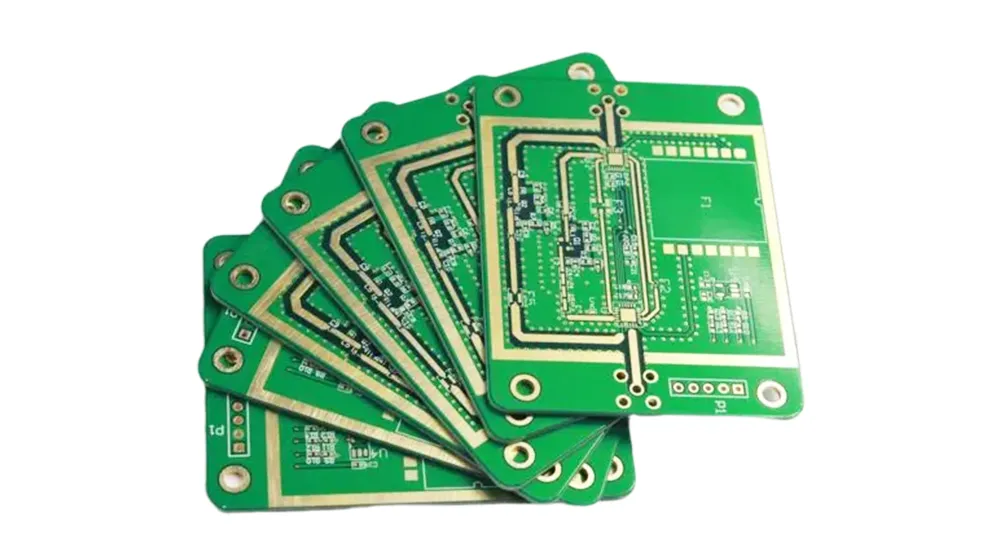
Advantages | Disadvantages |
---|---|
Low cost and wide availability | Poor thermal conductivity (0.3–0.4 W/mK) |
Excellent design flexibility for multilayer boards | Limited temperature resistance (170°C max) |
Mature manufacturing processes | Signal integrity challenges at high frequencies |
Lightweight construction | Requires additional thermal management |
How to Choose Between Metal Core PCB and FR4 PCB
1. Choose Metal Core PCB When:
High Power Density Applications
- LED lighting systems requiring prolonged operation at high temperatures
- Power electronics with >2W per square inch dissipation
- Automotive and industrial relays requiring thermal efficiency
Harsh Environment Requirements
- High-vibration applications where components must remain secure
- Systems requiring electromagnetic shielding
- Applications where secondary cooling would compromise design constraints
2. Choose FR4 PCB When:
Standard Electronic Applications
- Consumer electronics (smartphones, computers, routers)
- General-purpose circuits where cost optimization is priority
- Prototyping and development phases
Complex Circuit Requirements
- Multilayer designs (8+ layers)
- High-frequency communications (with appropriate FR4 grades)
- Applications where rapid design
3. Decision Framework
Consider these key factors in your selection process:
- Power Dissipation: >2W/sq inch typically requires MCPCB
- Operating Temperature: >85°C ambient favors metal core
- Budget Constraints: High-volume cost-sensitive designs favor FR4
- Reliability Requirements: Mission-critical applications benefit from MCPCB thermal advantages
- Manufacturing Timeline: FR4 offers faster prototype-to-production cycles
Environmental Impact and Sustainability Considerations
As the electronics industry faces increasing pressure to reduce environmental impact, the sustainability profiles of PCB substrates become crucial factors in material selection. Electronic waste (e-waste) production was approximately 7.3 kg per person per year in 2019 and is predicted to reach 74 Mt in 2030, being the fastest-growing class of waste, with PCBs waste making up to 42% of the total e-waste weight.
1. FR4 Environmental Challenges
Traditional FR4 substrates present significant environmental concerns due to their thermoset nature and chemical composition. FR4 is almost impossible to recycle or reuse, as the irreversibly cured epoxy-glass composite cannot be broken down for material recovery. The material contains halogenated flame retardant, which causes cancer and disrupts neurological function in humans and animals.
Key environmental issues with FR4
- Non-recyclable thermoset structure
- Contains brominated flame retardants (BFRs) that release toxic compounds
- Petroleum-based epoxy resins contribute to carbon footprint
- Limited end-of-life options beyond landfilling
2. Metal Core PCB Sustainability Advantages
MCPCBs offer superior environmental profiles primarily due to their metal substrate composition. Aluminum and copper cores are highly recyclable materials, enabling recovery of valuable resources at end-of-life. The thermal efficiency of MCPCBs can also contribute to overall system energy savings by reducing cooling requirements.
Environmental benefits of MCPCBs
- High recyclability of aluminum and copper substrates
- Reduced system-level energy consumption through better thermal management
- Elimination of secondary heat sinks reduces material usage
- Lower component failure rates extend product lifespan
Emerging Sustainable Alternatives
The industry is actively developing environmentally friendly PCB materials to address sustainability concerns. Researchers at the University of Washington have developed circuit-board laminate based on vitrimer material that’s easily recycled and can be reused, with researchers able to recover 98% of the vitrimer and 100% of the glass fiber.
Other innovations include bio-based substrates using renewable materials like PLA (poly-lactic acid) and natural fibers, offering compostable alternatives to traditional substrates.
Hybrid Solutions and Innovative Design Approaches
Modern electronic designs increasingly require solutions that optimize both thermal performance and cost-effectiveness. Rather than choosing exclusively between MCPCB and FR4 technologies, innovative hybrid approaches can leverage the strengths of both materials within single designs.
1. Selective Metal Core Integration
This approach involves using metal core sections only in high-heat areas while maintaining FR4 for the remainder of the design. Key implementation strategies include:
Thermally Critical Zone Design
- Metal core substrates positioned directly under high-power components
- FR4 sections for signal processing and low-power circuits
- Thermal bridges connecting heat sources to metal core areas
Multi-Substrate Assembly
- Mechanical integration of MCPCB modules with FR4 main boards
- Thermal interface materials optimizing heat transfer between substrates
- Flexible interconnects accommodating different thermal expansion rates
2. Advanced Thermal Management Techniques
Embedded Metal Heat Spreaders
Integration of metal plates or heat spreaders within FR4 stackups provides enhanced thermal performance without full MCPCB conversion. This approach maintains FR4’s electrical advantages while addressing thermal limitations through:
- Embedded aluminum or copper planes in multilayer FR4 designs
- Thermal via arrays providing vertical heat conduction paths
- Strategic copper pour optimization for heat spreading
Thermally Enhanced FR4 Variants
Specialized FR4 formulations incorporating thermally conductive fillers can achieve thermal conductivity improvements while maintaining standard processing compatibility:
- Ceramic-filled FR4 achieving 1.0+ W/mK thermal conductivity
- Graphene-enhanced composites providing directional thermal paths
- Thermally conductive prepreg materials for improved interlayer heat transfer
3. Cost-Optimized Hybrid Strategies
Selective Component Placement
Strategic component positioning enables thermal optimization without full substrate conversion:
- Heat-generating components clustered in metal core zones
- Thermal isolation techniques preventing heat migration to sensitive circuits
- Optimized copper weight distribution balancing thermal and electrical performance
Modular Design Approaches
System-level design strategies can optimize material usage across product architectures:
- Separating thermal and electrical functions into dedicated modules
- Standardized interface designs enabling mixed substrate assemblies
- Scalable thermal solutions adapting to power requirement variations
These hybrid approaches enable engineers to achieve optimal price-performance balance while addressing specific application requirements that neither pure MCPCB nor FR4 solutions can efficiently solve.
Conclusion
The choice between metal core PCB and FR4 PCB ultimately depends on balancing thermal requirements, cost constraints, and application-specific needs. MCPCBs excel in high-power, thermal-sensitive applications where superior heat dissipation justifies higher material costs. FR4 remains the optimal choice for cost-effective, general-purpose electronics where thermal management is less critical.
For applications requiring both thermal performance and cost optimization, hybrid approaches using thermal vias, copper pours, or selective metal core integration may provide balanced solutions. As environmental considerations become increasingly important, the recyclability advantages of metal core substrates and emerging bio-based alternatives will likely influence future material selection decisions.
Need expert PCB manufacturing guidance? Haoyue Electronics combines advanced substrate technologies with precision manufacturing processes, offering comprehensive design support to help you select the optimal PCB solution for your specific application requirements.
From prototype to production — we help hardware teams cut costs, improve yields, and scale faster. Let’s make your next product a success!