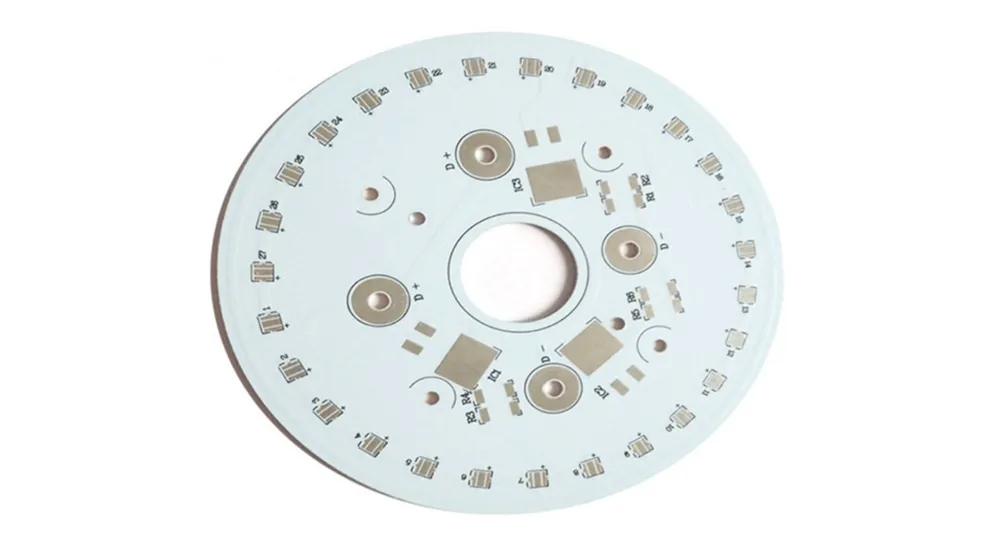
Understanding Metal Core PCB Technology and Construction
Metal Core PCB represents a significant advancement in thermal management technology. Unlike conventional PCBs that use fiberglass substrates, MCPCB incorporates a metal base layer that serves as an efficient heat conductor while maintaining electrical isolation.
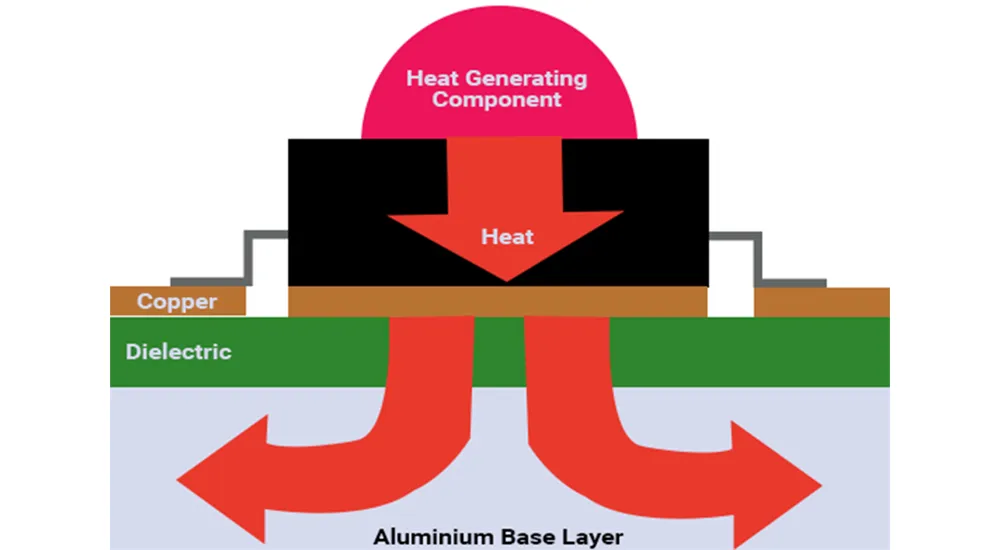
Core Structure Components
The typical metal core PCB consists of four essential layers working in harmony:
- Metal Base Layer
Usually constructed from aluminum, copper, or steel alloys, this foundation provides mechanical support and primary heat conduction. Aluminum substrates offer thermal conductivity ranging from 1.0–3.0 W/mK, while copper-based options can achieve 150–400 W/mK for extreme applications. - Dielectric Layer
This specialized insulating material enables heat transfer while maintaining electrical isolation. Advanced thermal interface materials include ceramic-filled polymers and thermally conductive epoxy resins. - Copper Circuit Layer
Standard copper foil creates the electrical pathways, with thickness typically ranging from 1–4 oz depending on current requirements. - Solder Mask
Protective coating that defines component placement areas and provides environmental protection.
Material Selection Criteria
Aluminum-based metal core PCB dominates the market due to its optimal balance of thermal performance, weight, and cost-effectiveness. For applications demanding superior heat dissipation, copper substrates deliver exceptional thermal conductivity but at higher material costs.
Ready to optimize your thermal management design? Our engineering team can help you select the ideal metal core PCB configuration for your specific requirements.
Key Advantages of Metal Core PCB Solutions
Metal Core PCB technology delivers multiple performance benefits that address critical challenges in high-power electronics design.
Superior Thermal Performance
The primary advantage lies in dramatically improved heat dissipation capabilities. Metal core PCB can reduce operating temperatures by 10-40°C compared to traditional FR4 boards, directly extending component lifespan and improving reliability.
*Thermal Conductivity Comparison
Material | Thermal Conductivity (W/mK) |
---|---|
Standard FR4 | 0.3 |
Aluminum MCPCB | 1.0 – 3.0 |
Copper MCPCB | 150 – 400 |
Enhanced Mechanical Stability
The metal substrate provides superior dimensional stability and resistance to thermal expansion. This characteristic proves essential for applications experiencing thermal cycling or mechanical stress.
Improved Electrical Performance
Better heat management translates to more stable electrical characteristics. Components maintain consistent performance parameters across wider temperature ranges, reducing drift and improving overall system reliability.
Compact Design Capabilities
Efficient heat dissipation often eliminates the need for external heat sinks or allows for smaller thermal management solutions. This advantage enables more compact product designs without compromising performance.
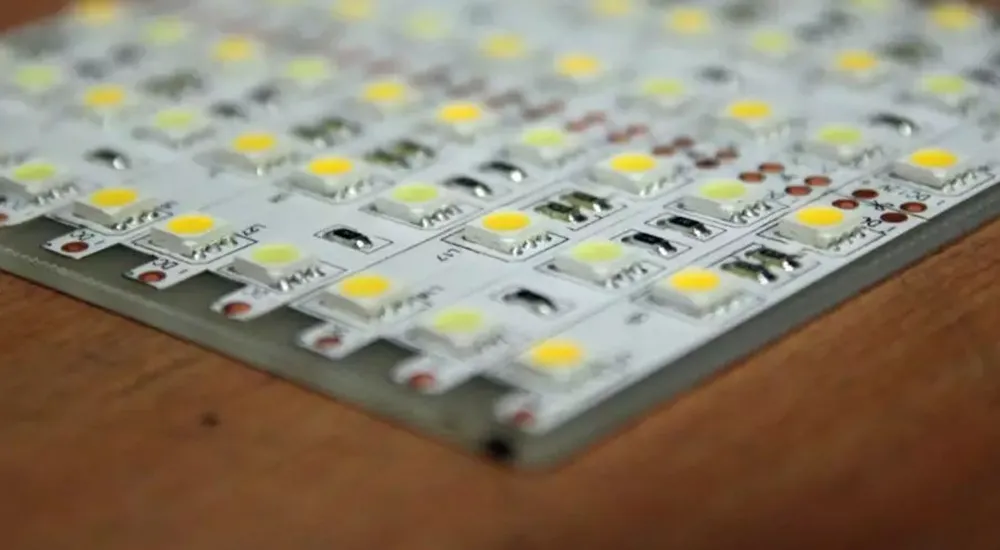
Metal Core PCB Applications Across Industries
Metal Core PCB technology finds application across diverse industries where thermal management is critical for performance and reliability.
LED Lighting Solutions
LED applications represent the largest market for metal core PCB technology. From automotive lighting to architectural fixtures, MCPCB enables higher LED power densities while maintaining optimal junction temperatures for maximum efficacy and lifespan.
Common LED Applications:
- Street and area lighting
- Automotive headlights and taillights
- High-bay industrial lighting
- Display backlighting systems
Automotive Electronics
The automotive industry increasingly relies on metal core PCB for power-dense applications including:
- Battery management systems
- Electric motor controllers
- Charging infrastructure
- LED lighting assemblies
- Power conversion modules
Power Electronics
Switch-mode power supplies, motor drives, and renewable energy systems benefit from MCPCB’s thermal advantages. Better heat management allows for higher power densities and improved efficiency.
RF and Microwave Applications
High-frequency applications utilize metal core PCB for improved thermal stability and reduced signal degradation in power amplifiers and transmitter circuits.
Considering metal core PCB for your next project? Contact our application engineers to discuss your thermal management requirements and explore optimal solutions.
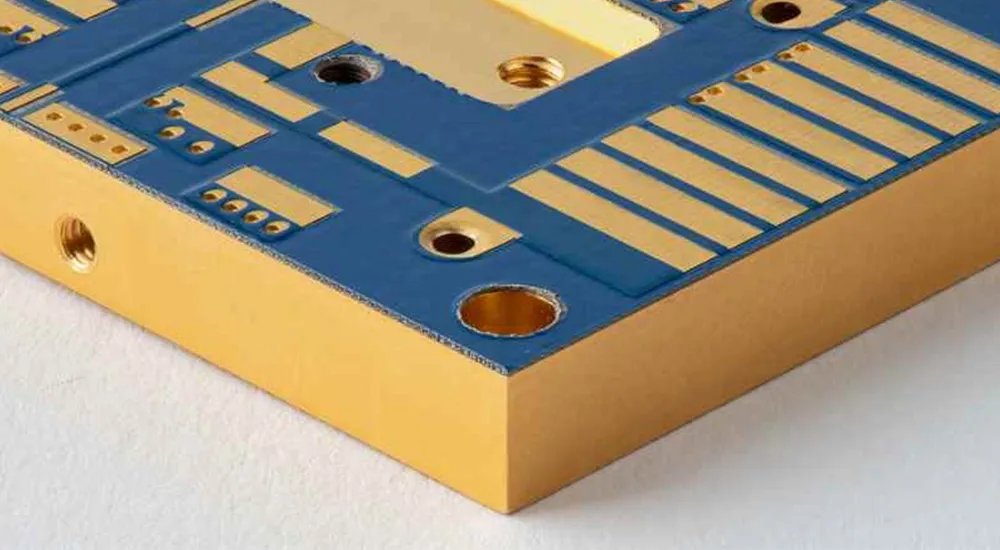
Design Considerations for Metal Core PCB
Successful metal core PCB implementation requires careful attention to several design parameters that differ from traditional PCB design practices.
Thermal Interface Optimization
Dielectric layer thickness directly impacts both thermal performance and electrical characteristics. Thinner dielectric layers improve heat transfer but may limit breakdown voltage, requiring careful balance based on application requirements.
Via and Drilling Considerations
Metal substrates require specialized drilling techniques and parameters. Via design must account for thermal expansion differences between copper and the metal base layer.
Component Placement Strategy
Strategic component placement maximizes thermal benefits by positioning heat-generating components directly above the metal base layer. Thermal modeling helps optimize layout for uniform heat distribution.
Assembly Process Adaptations
Soldering profiles may require adjustment to accommodate the increased thermal mass of metal core PCB. Proper preheating ensures reliable solder joint formation.
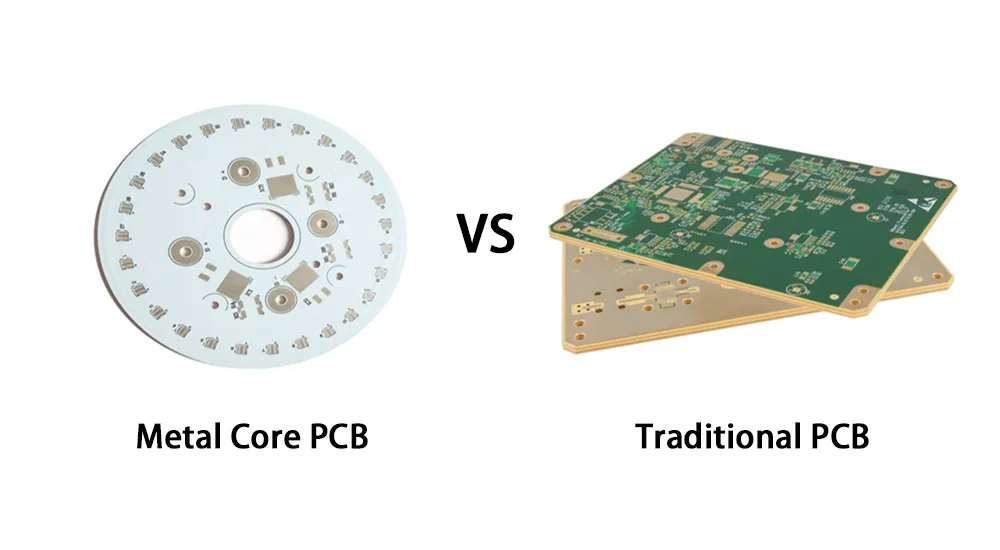
Metal Core PCB vs Traditional PCB Comparison
Understanding the performance differences helps determine when metal core PCB justifies the additional investment.
Thermal Performance Analysis
Metal core PCB delivers 3–10x better thermal conductivity compared to FR4 substrates. This improvement translates to significantly lower component operating temperatures and extended operational life.
Cost-Benefit Evaluation
While MCPCB material costs exceed traditional PCB, the total system cost often decreases through:
- Reduced heat sink requirements
- Smaller enclosure possibilities
- Improved reliability and reduced warranty costs
- Extended product lifespan
Reliability Improvements
Lower operating temperatures directly correlate with improved MTBF (Mean Time Between Failures). Studies show that every 10°C temperature reduction can double component lifespan.
Design Flexibility
Metal core PCB enables higher power densities and more compact designs, providing greater flexibility in product development while maintaining thermal integrity.
Selecting the Right Metal Core PCB Solution
Choosing the optimal metal core PCB requires evaluation of multiple technical and economic factors specific to your application.
Thermal Requirements Assessment
Begin by quantifying your thermal management needs:
- Maximum power dissipation
- Acceptable component temperatures
- Ambient operating conditions
- Thermal cycling requirements
Material Selection Guidelines
Aluminum Substrate: Ideal for cost-sensitive applications with moderate thermal requirements (1-3 W/mK)
Copper Substrate: Best choice for extreme thermal applications requiring maximum heat dissipation (150-400 W/mK)
Steel Substrate: Specialized applications requiring magnetic properties or extreme mechanical strength
Dielectric Layer Options
Standard dielectric materials work for most applications, while specialized high-thermal-conductivity options serve demanding requirements. High-voltage applications may require thicker dielectric layers.
Manufacturing Partner Selection
Success depends on working with experienced metal core PCB manufacturers who understand the unique processing requirements. Look for partners offering:
- Proven MCPCB manufacturing capabilities
- Design support and thermal modeling
- Quality certifications (ISO 9001, IPC standards)
- Application-specific experience
At Haoyue Electronics, we specialize in metal core PCB manufacturing and assembly services. Our experienced team provides comprehensive support from design optimization through volume production, ensuring your thermal management challenges are solved efficiently and cost-effectively.
Quality and Testing Considerations
Reliable metal core PCB requires rigorous testing including:
- Thermal resistance measurement
- Dielectric breakdown testing
- Thermal cycling validation
- Mechanical stress testing
Metal Core PCB technology continues advancing to meet the evolving demands of high-power electronics. As component power densities increase and product sizes shrink, MCPCB provides the thermal management foundation necessary for reliable, high-performance designs.
Ready to implement metal core PCB in your next project? Our engineering team stands ready to help you optimize your thermal management solution and achieve superior performance results. Contact us today to discuss your specific requirements and discover how metal core PCB can transform your product’s capabilities.
From prototype to production — we help hardware teams cut costs, improve yields, and scale faster. Let’s make your next product a success!