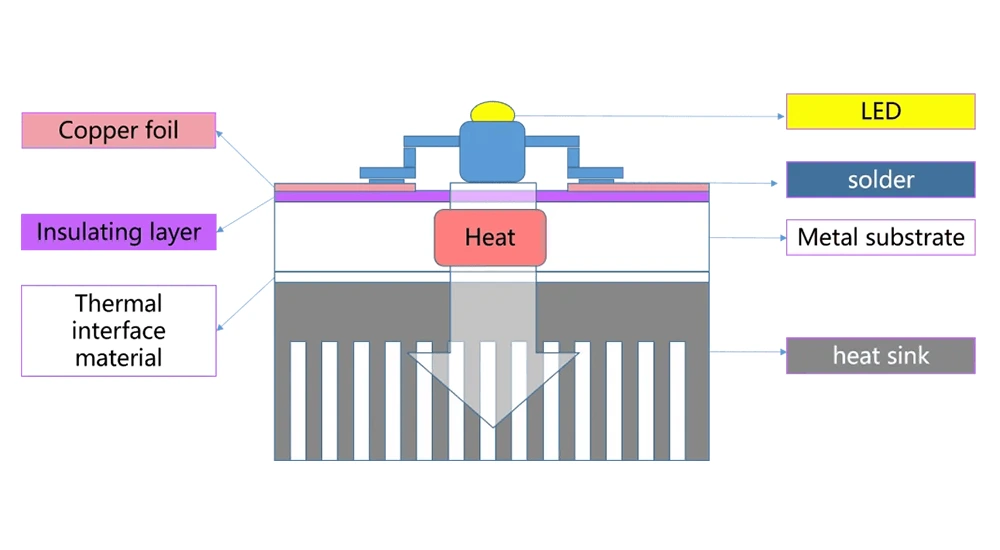
Thermal Conductivity Fundamentals in MCPCB Technology
Metal core PCBs achieve thermal conductivity values far exceeding traditional FR4 substrates. Standard FR4 offers only 0.3–0.4 W/mK, while metal core substrates deliver:
- Aluminum core: 150–240 W/mK
- Copper core: 385–400 W/mK
- Aluminum nitride ceramic: 170–320 W/mK
This 500–1000× improvement enables effective heat dissipation in power-dense applications. The MCPCB structure comprises three essential layers: metal substrate, thermally conductive dielectric, and copper circuit layer. The dielectric layer, typically 50–200μm thick with thermal conductivity of 1.0–12 W/mK, maintains electrical isolation while facilitating heat transfer.
At Haoyue Electronics, we utilize advanced dielectric materials achieving up to 8 W/mK thermal conductivity, ensuring optimal performance for demanding thermal applications.
Critical Design Parameters for Thermal Performance
Effective MCPCB thermal design requires careful optimization of multiple parameters:
Dielectric Selection: High-performance dielectrics balance thermal conductivity with electrical isolation. Thinner layers reduce thermal resistance but must maintain adequate breakdown voltage. Modern formulations achieve 3–8 W/mK while meeting UL94 V-0 flammability ratings.
Core Material and Thickness: Aluminum cores (1.0–3.0 mm typical) offer cost-effective thermal management for most applications. Copper cores provide maximum thermal performance for extreme power densities but increase cost and weight. Selection depends on specific thermal requirements and budget constraints.
Thermal Via Implementation: Properly designed thermal vias create efficient heat paths from components to the metal core. Via diameter, spacing, and fill material significantly impact thermal resistance. Filled vias using thermally conductive epoxy or electroplated copper minimize thermal bottlenecks.
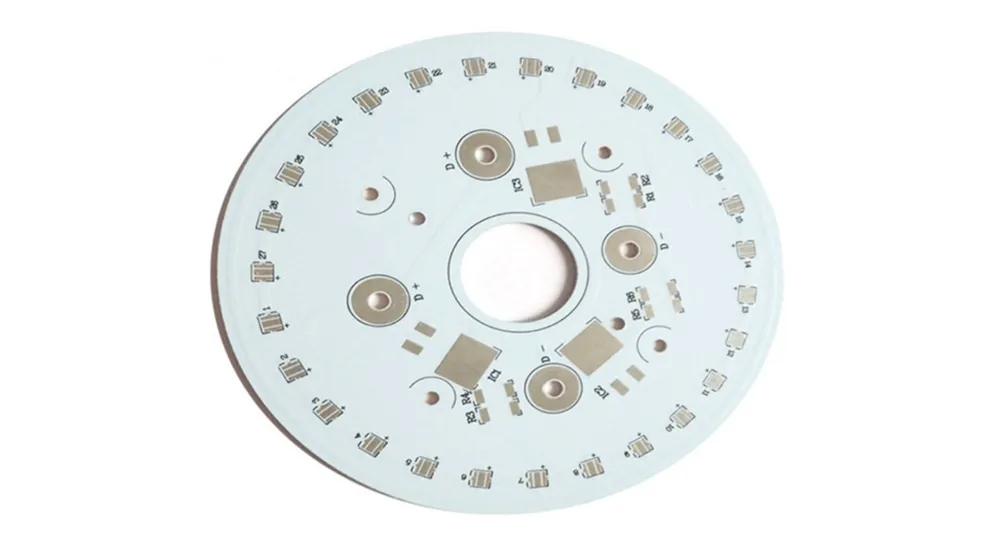
Optimization Strategies for Maximum Heat Dissipation
Strategic design approaches maximize MCPCB thermal performance:
Component Placement: Position high-power components directly over metal core areas with minimal dielectric thickness. Group heat-generating devices to create concentrated thermal zones with dedicated cooling paths.
Copper Distribution: Maximize copper coverage on circuit layers to enhance lateral heat spreading. Large copper polygons connected to thermal pads distribute heat before it reaches the metal core, reducing junction temperatures.
Thermal Interface Design: Direct thermal paths from components to heatsinks require careful attention to surface finishes and interface materials. Haoyue Electronics offers specialized surface treatments including hard anodization and selective plating to optimize thermal coupling.
Edge Plating Solutions: For external heatsink mounting, wraparound edge plating extends the metal core to PCB edges. This technique, perfected through our advanced manufacturing processes, creates zero-resistance thermal paths for LED and power applications.
Advanced Applications and Manufacturing Considerations
Modern MCPCB applications demand increasingly sophisticated thermal solutions:
Embedded Copper Technology: Direct copper embedding beneath high-power components achieves thermal resistance below 0.1°C/W. This technique requires precise manufacturing control to maintain layer registration and dielectric integrity.
Hybrid Constructions: Combining metal cores with localized thermal enhancements addresses non-uniform power distributions. Selective thick copper, embedded coins, and varied dielectric thickness optimize thermal performance while controlling costs.
Quality Assurance: Thermal performance verification requires specialized testing including thermal impedance measurement and infrared imaging. Our manufacturing process includes 100% electrical testing and thermal sampling to ensure consistent performance.
The evolution toward higher power densities in automotive electronics, 5G infrastructure, and solid-state lighting continues driving MCPCB innovation. Next-generation materials including diamond-filled composites and graphene-enhanced dielectrics promise thermal conductivity exceeding 50 W/mK.
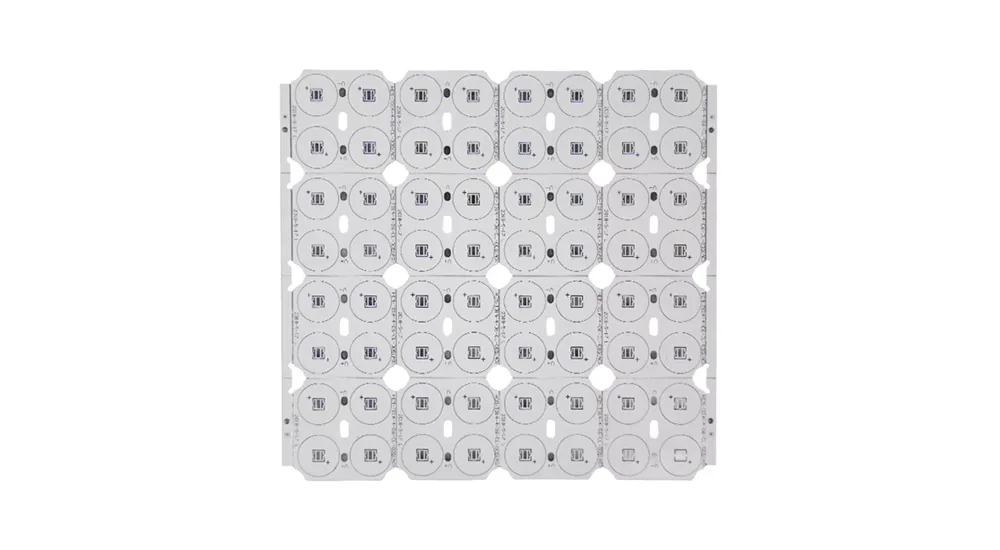
Partner with Thermal Management Experts
Selecting the right metal core PCB solution requires balancing thermal performance, reliability, and cost. Haoyue Electronics combines advanced manufacturing capabilities with thermal design expertise to deliver optimized MCPCB solutions. Our engineering team provides thermal modeling, design review, and prototype validation services to ensure your products meet thermal requirements.
Whether developing high-brightness LED modules requiring 5W/mK dielectric performance or automotive power modules demanding copper core substrates, we deliver precision-manufactured MCPCBs with consistent quality. Our ISO 9001 and IATF 16949 certified facilities maintain strict process controls ensuring reliable thermal performance in production volumes.
Ready to solve your thermal management challenges? Contact our engineering team to discuss your metal core PCB requirements. We provide detailed thermal analysis, material recommendations, and design optimization support to maximize your product’s thermal performance. Request a quote today to start your next high-power project with confidence.
From prototype to production — we help hardware teams cut costs, improve yields, and scale faster. Let’s make your next product a success!