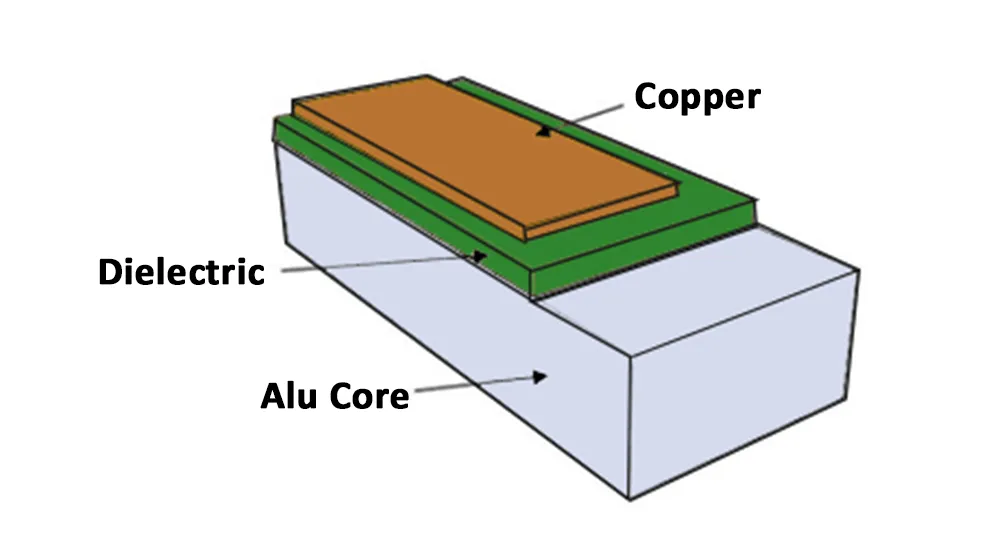
Metal core PCB stack-up design determines thermal success in high-power applications exceeding 150°C junction temperatures. Unlike FR4 substrates (0.3 W/mK), metal core configurations achieve 1.0-12 W/mK thermal conductivity through engineered material interfaces and optimized layer arrangements.
Critical Fact: Thermal failures cause 55% of high-power electronic failures. Proper metal core PCB stack-up optimization delivers superior reliability and performance.
Metal Core PCB Stack-Up Fundamentals and Thermal Physics
Core Material Properties and Selection Criteria
Aluminum 5052 H32: Thermal conductivity 138 W/mK, CTE 25 ppm/°C, yield strength 193 MPa. Industry standard for cost-effective applications.
Aluminum 6061 T6: Thermal conductivity 167 W/mK, yield strength 276 MPa. Superior machinability for complex geometries and precision drilling.
Copper C110: Thermal conductivity 386 W/mK, CTE 17 ppm/°C, density 8.96 g/cm³. Premium choice for maximum thermal performance with weight/cost considerations.
Material | Thermal Conductivity (W/m·K) | CTE (ppm/°C) | Yield Strength (MPa) | Density (g/cm³) |
---|---|---|---|---|
5052 H32 | 138 | 25 | 193 | 2.68 |
6061 T6 | 167 | 23.6 | 276 | 2.70 |
C110 Cu | 386 | 17 | 210 | 8.96 |
Thermally Conductive Dielectric Engineering
Modern dielectrics use aluminum oxide (Al₂O₃) filled epoxy achieving 1.5–3.0 W/mK thermal conductivity. Advanced boron nitride (BN) formulations reach 8–12 W/mK while maintaining >3000V breakdown voltage.
Thickness optimization: Rth = t / (k·A). Practical range 50–150 μm, with 75 μm optimal for electrical isolation (>2500V) and thermal resistance minimization.
Adhesive requirements: Tg >150°C, thermal conductivity 1–2 W/mK, peel strength >9 lb/in after thermal cycling.
Engineering Reality: Achieving optimal dielectric performance requires specialized equipment and materials characterization that most design teams underestimate.
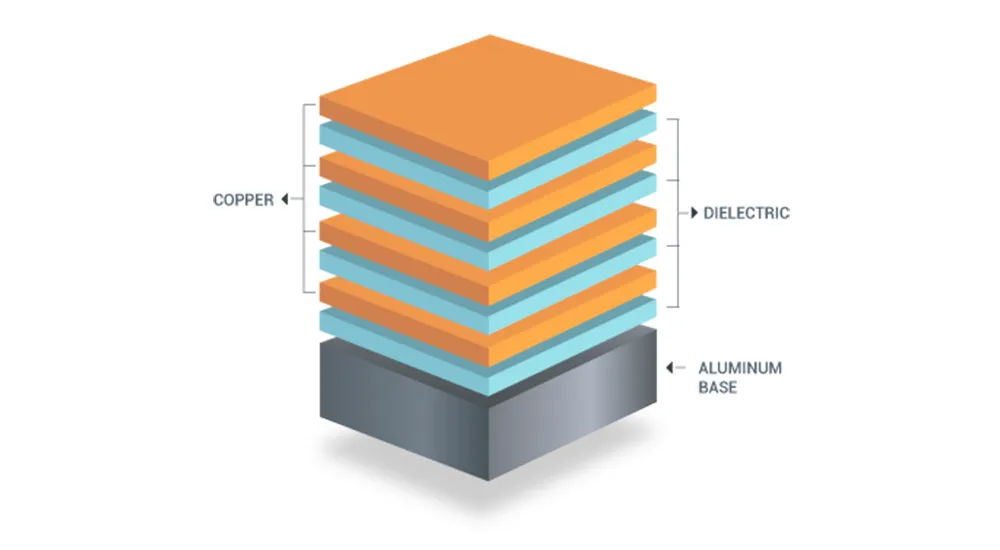
Advanced Stack-Up Configurations and Design Calculations
Symmetrical Multi-Layer Architecture
Symmetrical design prevents warpage: ΣCu(top) = ΣCu(bottom) within ±10% for thermal cycling stability (-40°C to +125°C).
CTE matching formula: αeffective = (α₁t₁ + α₂t₂ + … + αₙtₙ)/(t₁ + t₂ + … + tₙ). Mismatched CTEs >5 ppm/°C cause delamination.
Standard thicknesses: Core 0.8–3.2 mm (1.5 mm typical for LED), prepreg accounts for thermal expansion during 180°C lamination.
Design Challenge: Stack-up optimization from prototype to production requires balancing thermal performance, cost, and manufacturing scalability—often demanding specialized expertise.
Thermal Via Integration and Isolation
PTH isolation clearance: PTH_diameter + 2 × (thermal_expansion + tolerance + safety) = 1.0–1.2 mm clearance for 0.2 mm vias.
Fill materials: Thermal conductivity <0.5 W/mK, density 1.2–1.4 g/cm³, compressive strength >80 MPa.
Thermal via spacing: P = 2.5 × √(Rth_target × k_substrate × t_dielectric) optimizes thermal performance with manufacturing feasibility.
Manufacturing Process Engineering and Quality Control
Precision Lamination Parameters
Process requirements: 200–400 psi pressure, 1°C/min ramp to 170°C, 90-minute hold, 2°C/min cooling.
Vacuum lamination: 28–29 inHg eliminates air voids, ensures <0.1% void content by cross-sectional analysis.
Temperature uniformity: ±2°C across panel prevents Tg and thermal conductivity variations.
Manufacturing Reality: Achieving consistent vacuum and temperature parameters requires industrial equipment and extensive process validation—often making specialized manufacturers more efficient.
Advanced Drilling and Machining
Drilling parameters: 15,000–25,000 RPM, feed 0.05–0.15 mm/rev. Diamond-coated tools extend life 3–5× vs. uncoated carbide.
Cooling requirements: Synthetic fluid at 5–10 L/min maintains substrate <60°C, prevents thermal stress cracking.
Precision requirements: ±0.05 mm positional tolerance for thermal vias, verified by CMM measurement.
Thermal Performance Validation
Thermal resistance measurement: ASTM D5470 methodology. Rth_jc = (Tj – Tc)/P under steady-state conditions (<0.1°C/min drift).
Equipment requirements: Calibrated thermocouples (Type K, ±0.5°C), controlled heat source, known thermal interface materials.
Thermal imaging: FLIR cameras with <0.1°C sensitivity, emissivity correction 0.85–0.95 for oxidized aluminum.
Testing Investment: Comprehensive thermal characterization requires precision equipment and trained personnel—manufacturers with full testing capabilities accelerate development timelines.
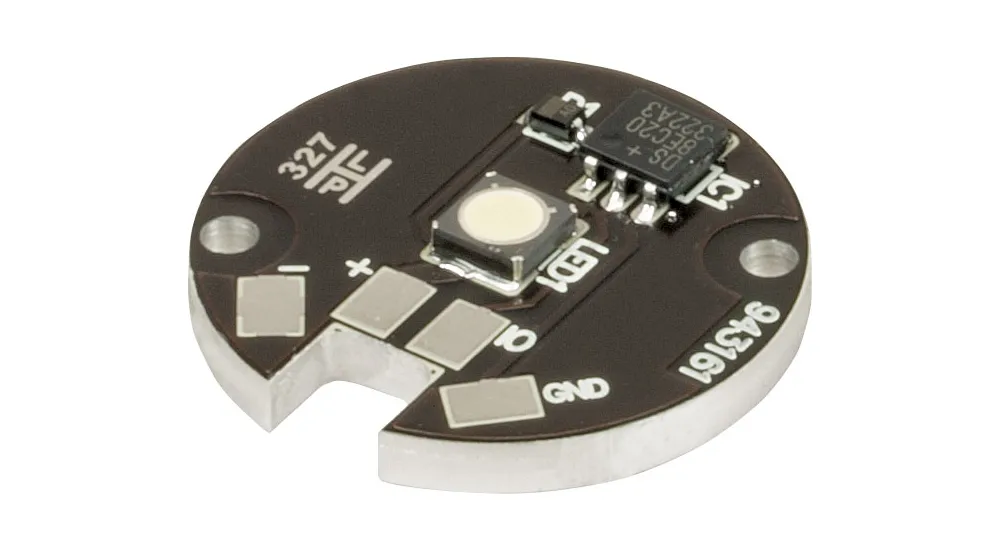
Application-Specific Design Optimization
High-Power LED Applications
COB LED arrays (50–200W/cm²) require thermal resistance <1.0°C·cm²/W. Demands: substrate >2.0mm thick, dielectric >5 W/mK thermal conductivity.
Phosphor management: Efficiency drops 0.5–1.0% per °C above 85°C junction temperature. Target <0.3°C·cm²/W thermal resistance for color stability.
Success Factor: Leading LED manufacturers achieve superior performance by partnering with metal core PCB specialists who optimize thermal design for luminous efficacy.
Power Electronics Integration
IGBT/MOSFET modules in EV applications handle >500A switching currents. Requirements: 4–6oz copper weight, trace width W = I/(k × t × ΔT), current density limits 10–15 A/mm².
High-frequency considerations: >50kHz switching creates skin effect. Skin depth δ = √(ρ/πfμ) = 0.21mm at 100kHz in copper, requiring optimized conductor geometry.
Partner with Haoyue Electronics for Precision Metal Core PCB Stack-Up Manufacturing
Advanced metal core PCB stack-up design demands manufacturing partners with thermal engineering expertise and precision process control. Haoyue Electronics combines thermal modeling with state-of-the-art equipment to deliver solutions exceeding performance specifications.
Why Choose Haoyue Electronics:
- Proven Track Record: 15+ years expertise, >99.5% on-time delivery, zero field failures in critical applications
- Advanced Capabilities: ASTM-certified testing, ±1°C lamination uniformity, 100% dimensional accuracy
- Engineering Support: Thermal design specialists reduce development time 30–50%
- Quality Assurance: ISO 9001:2015 certified with full traceability and statistical process control
- Cost Optimization: Competitive pricing with flexible volume scalability
Take Action: Contact Haoyue Electronics for complimentary thermal design consultation. Our engineering team will analyze your requirements and demonstrate how our metal core PCB stack-up expertise optimizes performance, reduces risk, and accelerates time-to-market.
Email your specifications or call our engineering hotline now—don’t let thermal limitations compromise your product’s performance.
From prototype to production — we help hardware teams cut costs, improve yields, and scale faster. Let’s make your next product a success!