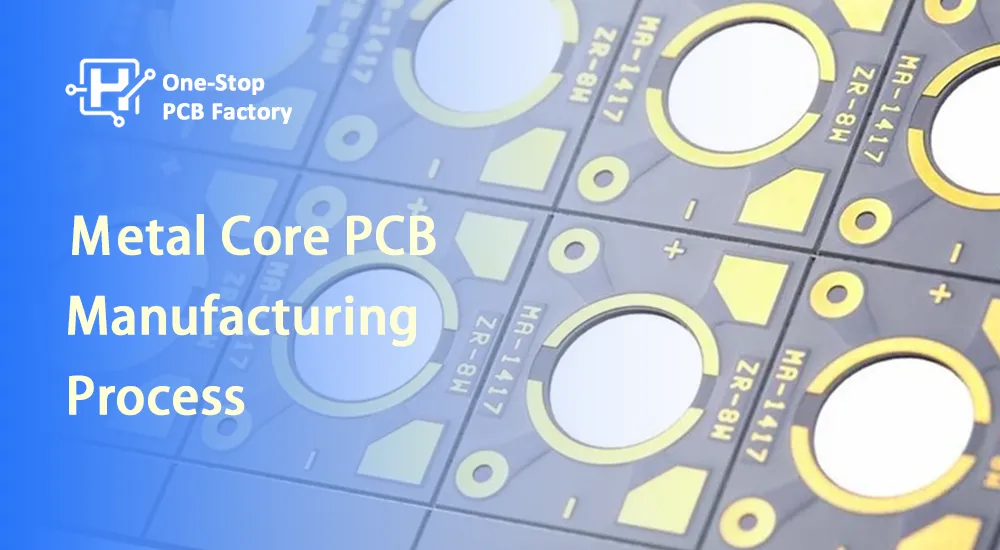
Understanding the sophisticated metal core PCB manufacturing process is essential for engineers developing high-performance thermal management solutions in LED lighting, power electronics, and automotive applications.
At Haoyue Electronics, we specialize in advanced MCPCB manufacturing with over a decade of experience serving high-tech industries worldwide. Our state-of-the-art facility combines precision manufacturing equipment with rigorous quality control systems to deliver thermal management solutions that exceed industry standards.
Fundamental MCPCB Architecture and Material Science
Precision-Engineered Layer Structure
The metal core PCB manufacturing process creates a sophisticated multi-layer assembly optimized for both thermal and electrical performance. The prepreg electrically isolates the copper circuitry layer from the metal layer and assists in heat transfer between the two layers. The prepreg disperses the heat generated by the components to the base metal at the earliest.
1. Metal Core Substrate
The foundation layer utilizes high-purity aluminum alloys (5052-H32, 6061-T6) or oxygen-free copper (C1100) with thicknesses ranging from 0.8mm to 3.2mm.
Aluminum: Best for cost-driven applications requiring thermal conductivity above 130 W/mK.
Copper: Ideal for applications where maximum heat dissipation is crucial. The substrate undergoes precision machining with tolerances maintained within ±0.05mm for dimensional accuracy.
2. Thermally Conductive Dielectric Layer
In conventional MCPCBs, there is a dielectric layer between the copper traces and the metal core, limiting the thermal conductivity to a range of 1 to 3 W/m·K. The dielectric thickness also plays a role in heat transfer. Usually, the thickness ranges from 2 mils to 6 mils. Advanced ceramic-filled polymers achieve thermal conductivity values of 2.0–3.0 W/m·K while maintaining electrical isolation resistance exceeding 10¹⁴ Ω·cm.
3. Copper Circuit Layer
MCPCB copper foil thickness can be 1–10 oz, with standard applications utilizing 1–2 oz copper. Heavy copper configurations (4–10 oz) accommodate high-current applications requiring enhanced current-carrying capacity and thermal dissipation.
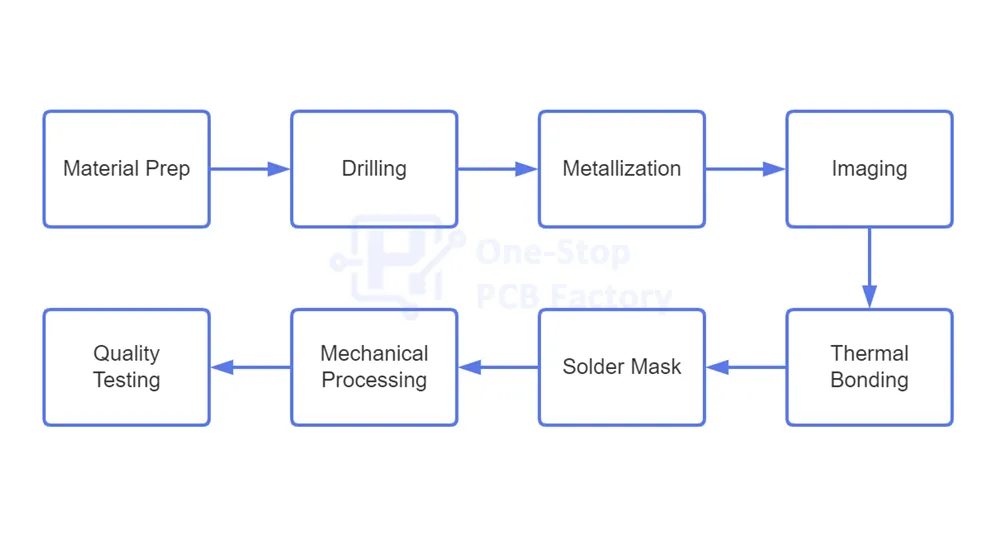
*Metal Core PCB Manufacturing Flow Chart
Comprehensive Metal Core PCB Manufacturing Process
Phase 1: Advanced Material Preparation and Surface Engineering
The metal core PCB manufacturing process begins with rigorous incoming material qualification. At Haoyue Electronics, our quality control laboratory utilizes coordinate measuring machines (CMM) with ±2μm accuracy for dimensional verification.
Our established relationships with premium material suppliers ensure consistent substrate quality, with aluminum substrates achieving Ra values below 1.6μm for optimal adhesion characteristics.
Chemical Surface Treatment
Our automated surface treatment line processes aluminum substrates with specialized chemical etching using chromate-free conversion coatings to achieve optimal surface energy (>40 dyne/cm) for dielectric adhesion.
Our precisely controlled process involves degreasing, micro-etching (0.5–1.0μm removal), and conversion coating application under monitored temperature (25–35°C) and pH (1.8–2.2) conditions, ensuring consistent adhesion performance across production batches.
Copper Foil Specification
We source electrolytic copper foil that meets stringent specifications for both electrical (>101% IACS conductivity) and thermal expansion matching. Our engineering team carefully selects materials with compatible CTEs to minimize stress between layers during thermal cycling.
Low-profile (LP) treatments provide superior adhesion reliability with peel strength exceeding 8 lb/in per IPC-4101 standards, validated through our comprehensive material testing protocols.
Phase 2: Precision Drilling and Mechanical Fabrication
High-Speed CNC Drilling
Our advanced drilling department features multiple CNC drilling systems utilizing carbide tools with specialized geometries for multi-material stacks. With capability for spindle speeds of 80,000–150,000 RPM and optimized feed rates for each material layer, we prevent delamination and ensure superior hole wall quality.
Our experienced operators maintain strict drilling parameters to ensure that drill bits remain sharp and pressure is appropriate to avoid drilling errors.
Micro-Via Technology
Haoyue Electronics’ laser drilling capabilities include state-of-the-art systems creating microvias (50–150μm diameter) with aspect ratios up to 1:1 for high-density interconnect applications. Our UV laser processing (355nm wavelength) provides precise material removal while preventing thermal damage to adjacent dielectric materials, enabling complex HDI designs that our customers depend on for space-constrained applications.
Hole Wall Preparation
Our plasma desmearing systems remove resin residues from via walls, followed by permanganate conditioning to create optimal surface morphology for metallization. Our process engineers maintain plasma power density of 2–4 W/cm² and exposure times of 3–8 minutes depending on dielectric material composition, ensuring consistent preparation for reliable plating adhesion.
Phase 3: Advanced Metallization and Plating Technology
Electroless Copper Deposition
Our automated plating lines utilize catalytic seeding with palladium-based activators to enable uniform copper nucleation on both organic and metallic surfaces. Haoyue Electronics’ electroless copper process, followed by our precisely regulated electrolytic plating, creates reliable interconnects essential for MCPCB performance.
Our controlled deposition rates of 3–5μm/hour provide conformable coverage with thickness uniformity within ±10%, validated through continuous statistical process control.
Electrolytic Copper Buildup
Our pattern plating capabilities achieve specified copper thickness with current density control between 15–25 ASF. Our chemistry management team maintains copper sulfate concentration at 210–250 g/L with sulfuric acid levels of 45–65 g/L for consistent deposition quality. Real-time monitoring systems ensure optimal plating conditions throughout production runs.
Through-Hole Plating Integrity
Haoyue Electronics’ specialized barrel plating process ensures 20–40μm copper thickness on hole walls with void-free coverage. Our quality assurance program includes thermal cycling qualification (−55°C to +125°C, 1000 cycles) to validate interconnect reliability under operational stress conditions, providing our customers with confidence in long-term product reliability.
Phase 4: Photolithographic Circuit Pattern Formation
High-Resolution Imaging
Laser direct imaging (LDI) systems with 10–20μm resolution capability enable precise pattern transfer on curved MCPCB surfaces. Dry film photoresist application utilizes lamination parameters of 105–115°C at 3–5 MPa pressure for optimal adhesion and conformability.
Precision Chemical Etching
Alkaline etching chemistry (cupric chloride-based) maintains etch factor >2.5:1 for fine feature definition. Over-etching narrows traces; under-etching leaves shorts between conductors. These issues often arise from aged chemistry or poor agitation. Spray pressure optimization (15–25 PSI) and temperature control (45–55°C) ensure uniform material removal across varying substrate thermal masses.
Advanced Strip and Clean
Photoresist removal utilizes environmentally compliant chemistry with complete residue elimination verified through surface energy measurements. Post-etch cleaning protocols prevent copper oxidation while protecting aluminum substrate integrity.
Phase 5: Critical Thermal Interface Processing
This phase distinguishes metal core PCB manufacturing from conventional fabrication through specialized thermal interface material (TIM) processing requiring precise parameter control. At Haoyue Electronics, this critical process utilizes our advanced lamination equipment and decades of process optimization experience.
Dielectric Material Application
Our controlled application systems handle thermally conductive prepreg materials, achieving thickness uniformity within ±5μm. Using our real-time pressure and temperature monitoring (300–600 PSI and 180–220°C), we optimize resin flow and layer bonding for superior thermal performance.
Our material expertise with advanced ceramic-filled systems provides thermal conductivity approaching 3.0 W/m·K while maintaining dielectric strength >3000V/mil.
Critical Lamination Process
Haoyue Electronics’ lamination department operates with modified parameters specifically optimized for MCPCB production: initial “kiss pressure” of 50–100 PSI, followed by our carefully controlled pressure ramping to 400–600 PSI.
Our experienced technicians understand that proper pressure progression is essential – starting with lower initial pressure (15–50 PSI) called “kiss pressure,” then ramping to full pressure (300–500 PSI) as the resin softens and cures, ensuring optimal layer adhesion and thermal interface performance.
Thermal Cycling Validation
Our comprehensive post-lamination qualification program includes thermal shock testing (-40°C to +150°C, 500 cycles minimum) and thermal impedance measurement using standardized JEDEC test methods. We validate that thermal resistance values meet customer specifications, typically achieving 0.5–2.0°C·cm²/W depending on application requirements, backed by our complete test data documentation.
Phase 6: High-Temperature Solder Mask Technology
Thermally Stable Formulations
Specialized solder mask chemistry withstands continuous operating temperatures up to 180°C with glass transition temperatures (Tg) exceeding 200°C. These boards have a thermal conductivity ranging from 1 W/mK to 9 W/mK and can withstand temperatures up to 400°C. UV-curable systems provide excellent adhesion to both copper circuits and exposed aluminum areas with peel strength >8 lb/in.
Precision Application Techniques
Screen printing utilizes mesh tensions of 25–35 N/cm with emulsion thickness optimized for uniform coverage. Cross-Sectional Analysis: Our automated microscopy systems allow us to conduct cross-sectional analysis to ensure void-free bonding and validate the dielectric thickness. Registration accuracy maintained within ±25μm ensures proper component clearances.
Surface Finish Compatibility
HASL, ENIG, and OSP surface finishes accommodate the differential thermal expansion between copper and aluminum substrates. Immersion processes utilize modified chemistry to prevent aluminum corrosion while achieving specified coating thickness and solderability performance.
Phase 7: Advanced Mechanical Processing
CNC Routing Optimization
Multi-spindle routing systems employ diamond-coated carbide tools specifically designed for abrasive aluminum substrates. Cutting parameters include spindle speeds of 24,000–36,000 RPM with feed rates of 1.5–3.0 m/min, achieving edge quality Ra <3.2μm while maintaining ±0.05mm dimensional tolerance.
V-Scoring Technology
Precision V-groove cutting utilizes tungsten carbide wheels with included angles of 30–90 degrees. Depth control systems maintain residual material thickness of 0.1–0.3mm for reliable depaneling while preserving structural integrity during assembly operations.
Integrated Hardware Solutions
CNC machining capabilities enable direct installation of threaded inserts, thermal interface mounting hardware, and custom mechanical features during fabrication. This integration reduces assembly complexity while ensuring optimal thermal interface contact.
Phase 8: Comprehensive Quality Validation
Electrical Performance Testing
Haoyue Electronics’ automated test equipment validates circuit continuity, isolation resistance (>100MΩ minimum), and electrical functionality across every production unit.
Our filled resin isolation process fully fills drilled holes with resin to isolate electrical connections between outer layers and the metal core. Our specialized test protocols account for capacitive coupling effects between circuits and grounded metal cores, ensuring complete electrical validation.
Thermal Performance Characterization
Our thermal testing laboratory measures thermal resistance (Rθ) as a key parameter in assessing heat conduction capability. Using JEDEC JESD51 standard thermal transient testing, we validate junction-to-case thermal resistance for customer applications.
Our thermal impedance measurements utilize 1ms-10s transient heating to characterize complete thermal pathways from component mounting to ambient heat rejection, providing customers with comprehensive thermal performance data.
High-Voltage Isolation Validation
Our dielectric testing capabilities ensure electrical safety between circuits and metal substrate with test voltages ranging from 1500V-4000V AC depending on application requirements. We monitor leakage current below 1μA maximum and perform partial discharge testing at 1.2x rated voltage to validate long-term insulation integrity, backed by our ISO 9001:2015 certified quality management system.
Advanced Metrology
Haoyue Electronics’ quality control department utilizes coordinate measuring machines with thermal compensation, providing dimensional validation within ±10μm accuracy.
Our surface roughness measurement capabilities ensure thermal interface mating surface quality, while automated optical inspection systems verify circuit integrity and component clearances. Complete documentation packages accompany every shipment, supporting customer qualification and traceability requirements.
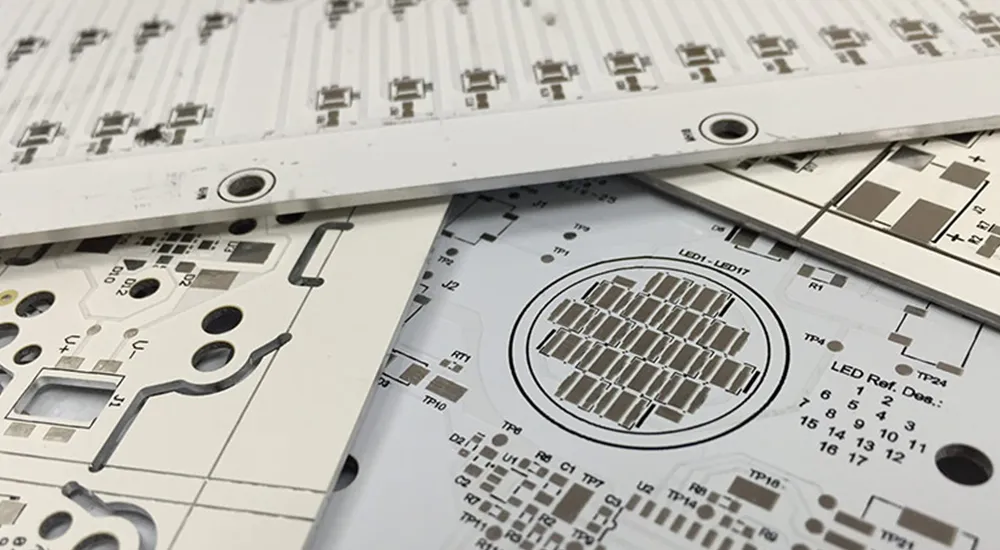
Advanced Engineering Considerations
Thermal Pathway Optimization
Metal core PCB manufacturing must strategically optimize thermal conduction pathways while maintaining electrical performance. A major factor to keep in mind during the design process of an MCPCB is to minimize the use of plated through-hole components.
Instead, implement SMT components. Thermal via arrays with 0.2-0.4mm diameter spacing create efficient heat transfer channels, while copper plane distribution balances current carrying capacity with thermal spreading.
Materials Science Integration
Modern metal core PCB manufacturing utilizes advanced metallurgy and polymer science. The coefficient of thermal expansion (CTE) represents the degree to which a material expands or contracts in response to temperature changes.
In MCPCBs, mismatched CTEs between the metal core and other layers can lead to structural issues. CTE matching between aluminum (23 ppm/°C) and copper (17 ppm/°C) requires specialized dielectric formulations with intermediate expansion characteristics.
Process Control Systems
Leading metal core PCB manufacturing facilities implement real-time process monitoring with statistical process control (SPC).
At Haoyue Electronics, our multi-stage vacuum presses remove 99.9% of air pockets and volatiles from laminate stacks, which is crucial for high-Tg and heavy copper boards where trapped air can lead to defects. Our automated parameter adjustment systems maintain consistent quality while accommodating material lot variations and environmental conditions.
*Haoyue Electronics' Advanced Manufacturing Capabilities
Capability | Specification |
---|---|
Substrate Size Range | 10mm x 10mm to 500mm x 400mm panels |
Copper Thickness | 1oz to 10oz (35μm to 350μm) with ±10% tolerance |
Metal Core Thickness | 0.8mm to 3.2mm aluminum or copper cores |
Minimum Via Size | 0.1mm (4 mil) diameter with 1:1 aspect ratio |
Layer Count | Single-layer to 4-layer MCPCB configurations |
Production Capacity | 50,000+ square meters monthly production capacity |
Industry Standards and Certification Requirements
Professional metal core PCB manufacturing adheres to rigorous industry standards including IPC-2221 for design guidelines, IPC-6012 for qualification requirements, and IPC-4101 for material specifications.
Peel Strength Testing: We perform rigorous peel strength testing, ensuring that our boards exceed IPC-4101 standards with an adhesion strength of at least 8 lb/in for FR-4. ISO 9001:2015 quality management systems ensure consistent process control and continuous improvement methodologies.
*Haoyue Electronics' Comprehensive Certification Portfolio
Category | Certification / Compliance |
---|---|
Quality Management | ISO 9001:2015 certified with annual third-party audits |
Environmental Standards | ISO 14001 environmental management certification |
Automotive Quality | IATF 16949 certification for automotive industry applications |
Safety Certifications | UL recognition for materials and processes |
RoHS Compliance | Full compliance with European environmental directives |
REACH Regulation | Complete material safety documentation and compliance |
Customer Benefits of Our Certification Approach:
- Streamlined customer qualification processes
- Reduced supply chain risk through verified quality systems
- Complete documentation packages supporting customer audits
- Continuous improvement culture driving performance enhancement
Emerging Technologies and Future Developments
Advanced metal core PCB manufacturing continues evolving to meet increasing performance demands.
However,with the use of COB MCPCB,as the dies directly contact the metal core,there is no such dielectric layer,resulting in the thermal conductivity of COB MCPCB being almost the same as that of the metal core material itself. Chip-on-board (COB) integration achieves thermal conductivity approaching base metal performance (>200 W/m·K) by eliminating traditional dielectric barriers.
Embedded component technologies integrate passive elements directly within MCPCB structures, reducing assembly complexity while improving thermal performance. Advanced materials research focuses on graphene-enhanced dielectrics and metal matrix composites for next-generation thermal management solutions.
Manufacturing Partner Selection Criteria
When evaluating metal core PCB manufacturing capabilities, critical factors include process certifications, thermal testing equipment, design-for-manufacturability expertise, and production scalability. Your manufacturer must be able to support your design complexity — whether it’s HDI, controlled impedance, via-in-pad, or metal-core PCBs.
Why Leading Companies Choose Haoyue Electronics:
Our customers consistently select us for MCPCB manufacturing because we combine state-of-the-art equipment with deep metallurgical expertise and proven production capabilities:
- Advanced Manufacturing Infrastructure: Over 50,000 sq ft facility with climate-controlled production environments and cutting-edge equipment
- Comprehensive Certifications: ISO 9001:2015, ISO 14001, IATF 16949, and UL certifications ensuring consistent quality and regulatory compliance
- Expert Engineering Support: Our experienced engineering team provides comprehensive thermal modeling services and DFM optimization to ensure manufacturable designs that meet performance requirements while maintaining cost-effectiveness
- Rapid Prototyping Capabilities: 5-day prototype turnaround with full production scalability from single units to high-volume manufacturing
- Global Supply Chain: Established relationships with premium material suppliers ensuring consistent quality and competitive pricing
- Customer Success Track Record: Over 500 successful MCPCB projects delivered to customers in automotive, LED lighting, power electronics, and telecommunications industries
Our commitment to technical excellence and customer partnership has made us the preferred MCPCB manufacturer for companies requiring exceptional thermal management solutions with guaranteed quality and on-time delivery.
Technical Innovation in Production Excellence
The complexity of metal core PCB manufacturing demands specialized knowledge integration across materials science, thermal engineering, and precision manufacturing.
Sequential Lamination: Ideal for complex 20+ layer boards, this method allows the use of mixed materials, such as FR-4 + Rogers® cores, to optimize both signal integrity and thermal performance.
Understanding these advanced process technologies enables informed engineering decisions when specifying thermal management solutions for demanding electronic applications requiring exceptional reliability and performance.
At Haoyue Electronics, we’ve invested over a decade in perfecting these complex, interdisciplinary technologies while maintaining the quality control systems necessary for consistent, reliable production.
Our comprehensive approach combines advanced materials science expertise, precision manufacturing technology, and thermal engineering knowledge to deliver MCPCB solutions that exceed customer expectations.
Partner with Haoyue Electronics for Your MCPCB Success
Modern metal core PCB manufacturing represents the convergence of advanced materials science, precision manufacturing technology, and thermal engineering expertise. Success in high-power electronic applications depends on selecting manufacturing partners who demonstrate mastery of these complex technologies while maintaining proven quality and delivery performance.
Ready to Optimize Your Thermal Management Design?
Whether you’re developing next-generation LED lighting systems, high-power automotive electronics, or advanced power conversion equipment, our MCPCB manufacturing expertise can help you achieve superior thermal performance while meeting cost and schedule objectives.
Contact Haoyue Electronics today to discuss your specific MCPCB requirements:
- Free Design Review: Our engineering team will evaluate your design for manufacturability and thermal optimization
- Rapid Prototyping: Get high-quality MCPCB prototypes in as little as 5 days
- Technical Consultation: Access our thermal modeling capabilities and material selection expertise
- Volume Production: Scalable manufacturing from prototypes to high-volume production
From prototype to production — we help hardware teams cut costs, improve yields, and scale faster. Let’s make your next product a success!