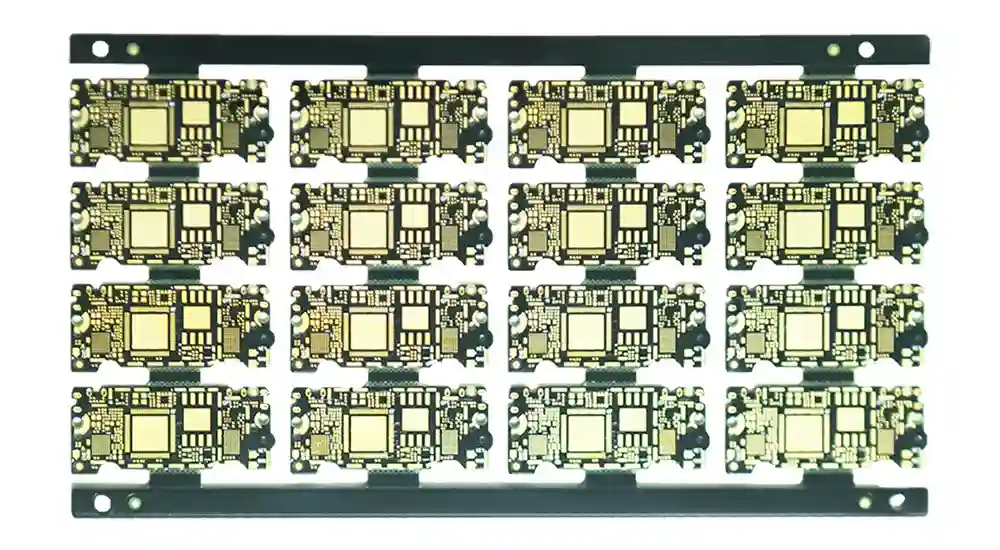
- Normal speed materials with dissipation factors greater than 0.012 suitable for applications up to 5 GHz.
- Medium speed materials with Df between 0.007-0.012 for applications up to 10 GHz.
- High speed materials with Df 0.003-0.007
- Very high speed materials with Df ≤ 0.002 for applications operating at 20-60 GHz.
Your material selection process should evaluate dielectric properties, thermal characteristics, mechanical requirements, and manufacturing considerations. Each parameter influences immediate performance and long-term reliability. This guide provides practical frameworks for choosing optimal materials based on specific application requirements.
Understanding HDI PCB Material Requirements and Performance Categories
1. Material Classification by Electrical Performance
Normal Speed and Normal Loss Materials
Normal speed FR4 materials exhibit higher dielectric loss and frequency-dependent dielectric constants. These materials suit applications up to 5 GHz where cost optimization takes priority over premium electrical performance. Isola 370HR represents this category with adequate functionality for standard digital applications below 1 GHz.
Medium Speed and Medium Loss Materials
Medium speed materials like Nelco N7000-2 HT offer flatter dielectric response and approximately half the loss of normal speed materials. These materials support applications up to 9 GHz and provide optimal balance between performance and cost for moderate-speed digital and lower microwave applications.
High Speed and Low Loss Materials
High speed materials such as Isola I-Speed feature flatter dielectric constants and reduced noise generation. These materials support frequencies to 15 GHz and are essential for high-speed digital interfaces, precision analog circuits, and moderate RF applications requiring superior signal integrity.
Very High Speed and Ultra-Low Loss Materials
Very high speed materials like Isola Tachyon 100G provide the flattest dielectric response and lowest loss characteristics. These materials support applications above 20 GHz and are necessary for millimeter-wave frequencies, minimal signal distortion requirements, and maximum dynamic range applications.
2. Essential Dielectric Properties for HDI Applications
Dielectric Constant Stability and Frequency Response
Dielectric constants typically range from 3.5 to 5.5 and decrease with increasing frequency. Select materials with stable dielectric constants across your operational frequency range to ensure consistent impedance control. Poor frequency stability causes impedance variations leading to signal reflections and timing skew.
Loss Tangent Considerations and Signal Attenuation
Loss tangent ranges from 0.02 to 0.001 and increases with frequency. Lower dissipation factors provide superior signal transmission and reduced power consumption. Signal attenuation accumulates over transmission line length, making loss tangent critical for extended routing or multiple layer transitions.
3. Thermal Management Considerations in Material Selection
Thermal Conductivity Requirements and Heat Dissipation
Standard PCB substrates exhibit thermal conductivity of 0.3 to 0.6 W/M-°C compared to copper at 386 W/M-°C. Applications with significant power dissipation require thermally enhanced materials with higher conductivity values to ensure adequate heat removal and component reliability.
Glass Transition Temperature and Processing Compatibility
Glass transition temperature defines the transition from rigid to softened state. Select materials with Tg exceeding 170°C for lead-free soldering compatibility and multiple reflow cycles. Higher Tg provides better dimensional stability during manufacturing and enhanced reliability during temperature excursions.
Coefficient of Thermal Expansion and Mechanical Stress
CTE mismatch creates mechanical stress during temperature cycling. Select materials with z-axis CTE below 40 ppm/°C for microvia reliability. CTE mismatch can cause via barrel cracking and component attachment failures over extended operational lifetimes.
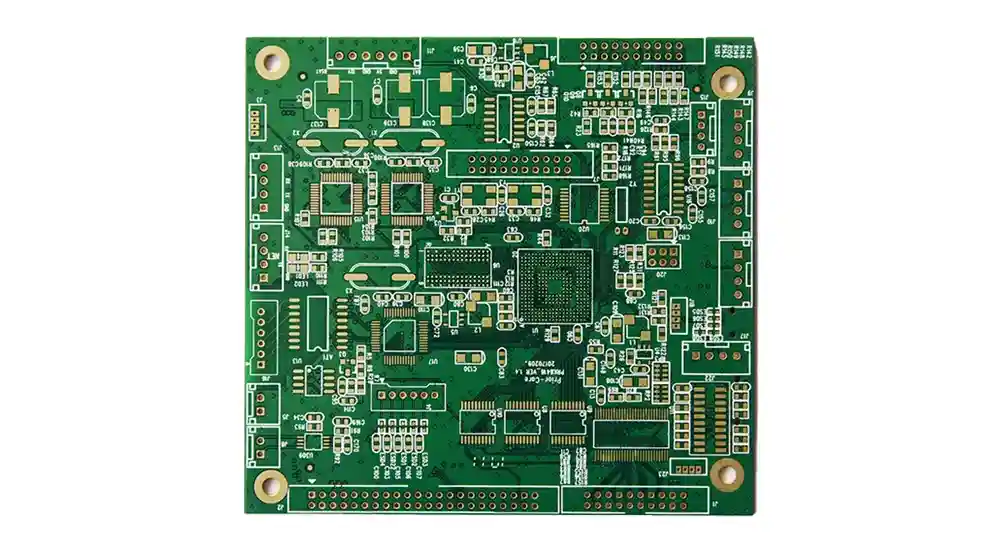
Application-Specific Material Selection Criteria
1. High-Frequency and RF Application Requirements
Material Properties for Microwave Performance
RF and microwave applications require the flattest Dk versus frequency response and minimal dielectric loss. Materials suitable for 20-60 GHz typically achieve dissipation factors ≤ 0.0021. PTFE-based materials provide required electrical performance but demand specialized processing compared to standard epoxy materials.
Substrate Construction and Fiber Weave Effects
PTFE-based materials may be available as unreinforced laminates, eliminating fiber weave effects but complicating processing. Densely woven glass weaves (1078, 1035, 3313, 1067) minimize fiber weave effects for applications sensitive to impedance variations and skew effects.
2. Digital High-Speed Application Considerations
Signal Integrity Requirements and Material Performance
High-speed digital applications require stable impedance control and minimal crosstalk. Medium-speed materials provide optimal balance for applications operating to 10 GHz. Faster edge rates demand better frequency stability and lower loss characteristics across the signal frequency spectrum.
Power Delivery and Signal Routing Considerations
Dense component placement requires materials supporting low-impedance power distribution while maintaining signal integrity. Select materials with appropriate dielectric constants for target impedances and adequate thermal performance for power dissipation requirements.
3. Automotive and Industrial Application Requirements
Environmental Durability and Long-Term Reliability
Automotive applications require 15-year operational lifetimes across -40°C to +125°C temperature ranges. Materials must withstand temperature cycling, vibration, humidity, and chemical exposure exceeding consumer electronics requirements while maintaining electrical and mechanical performance.
Certification and Qualification Requirements
Industrial applications demand enhanced chemical resistance and mechanical durability. Automotive-qualified materials typically provide reliability margins for demanding industrial applications. Verify materials meet relevant industry standards and suppliers provide required documentation for certification processes.
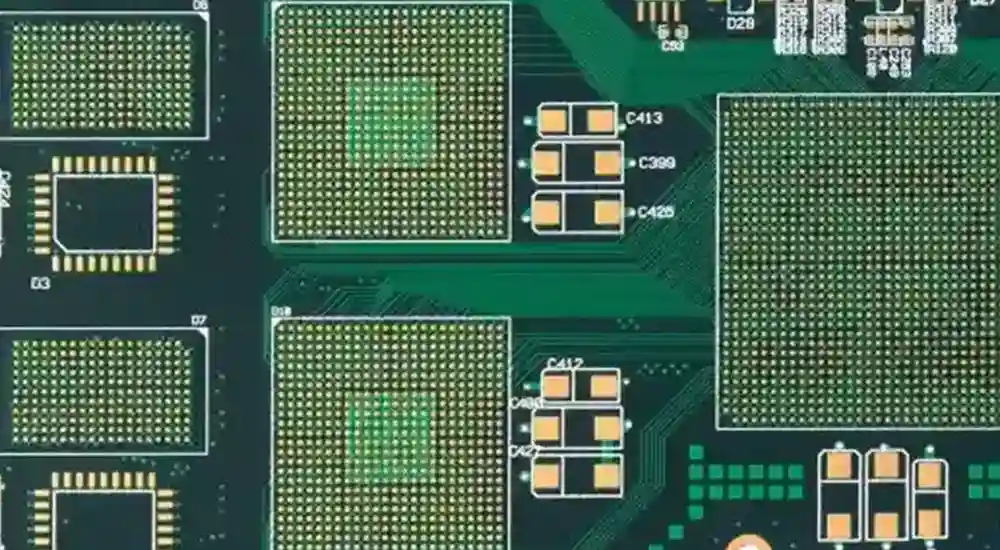
Practical Material Selection Framework and Decision Process
1. Establishing Performance Requirements and Constraints
Defining Electrical Performance Specifications
Document operating frequency range, signal integrity requirements, power dissipation levels, and environmental conditions. These specifications guide material category evaluation and eliminate options unable to meet fundamental requirements. Include worst-case conditions and margin requirements for reliable performance.
Manufacturing Capability and Process Constraints
Automotive manufacturers require 75μm minimum line spacing, two-layer build-up capability, CPK ≥ 1.33, and CMK ≥ 1.67. Understand manufacturing partner capabilities and certification requirements to ensure material compatibility with available production processes and quality standards.
Cost Analysis and Economic Considerations
Evaluate total cost implications including material cost, manufacturing complexity, yield impacts, and long-term reliability. Consider lifecycle costs including field reliability, warranty costs, and obsolescence risks. Established suppliers may justify cost premiums through reduced risk and superior support.
2. Material Evaluation and Testing Methodology
Electrical Characterization and Performance Validation
Conduct electrical testing at relevant frequencies to verify materials meet performance requirements under actual operating conditions. Test vehicles replicating critical design elements provide more accurate performance predictions than relying solely on material specifications.
Thermal and Mechanical Testing Requirements
Evaluate thermal conductivity, glass transition temperature, and thermal cycling performance for your thermal environment. Accelerated aging tests provide insight into long-term stability. Address both processing stresses and operational stresses throughout product lifetime.
Manufacturing Process Compatibility Assessment
Verify laser drilling characteristics, lamination behavior, and plating compatibility. Five laser systems (UV/Excimer, UV/YAG, CO2, YAG/CO2, CO2/TCO2) require specific material wavelength compatibility. Ensure material behavior throughout entire manufacturing sequence maintains production efficiency and quality.
3. Supplier Selection and Partnership Considerations
Material Source Evaluation and Supply Chain Management
Balance material performance, cost competitiveness, and supply chain reliability. Authentic laminates from established brands (Isola, Nelco) or equivalent Chinese suppliers (SY, KB) enable cost optimization without performance compromise. Evaluate technical capability, quality systems, and geographic coverage.
Technical Support and Application Engineering Services
Suppliers offering design guidance, process optimization, and troubleshooting support provide value beyond pricing. Strong technical teams and comprehensive support accelerate development cycles and improve manufacturing yields, particularly valuable for complex HDI applications.
Long-Term Partnership and Technology Roadmap Alignment
Evaluate supplier technology roadmaps and development capabilities for future requirements. Suppliers investing in advanced materials and manufacturing capabilities better support evolving needs. Consider lead times, inventory requirements, and backup supplier qualification for supply continuity.
Haoyue Electronics combines extensive HDI PCB manufacturing experience with comprehensive material characterization capabilities to support optimal material selection for diverse applications. With a relentless commitment to engineering excellence, our team provides in-depth material selection guidance, process optimization, and quality assurance to ensure flawless performance and long-term reliability.
Whether you’re developing next-generation solutions for telecommunications, automotive, industrial, or consumer electronics, we’re here to help you bring your innovations to life. Partner with Haoyue Electronics and unlock the full potential of your HDI designs — with confidence, speed, and precision.
From prototype to production — we help hardware teams cut costs, improve yields, and scale faster. Let’s make your next product a success!