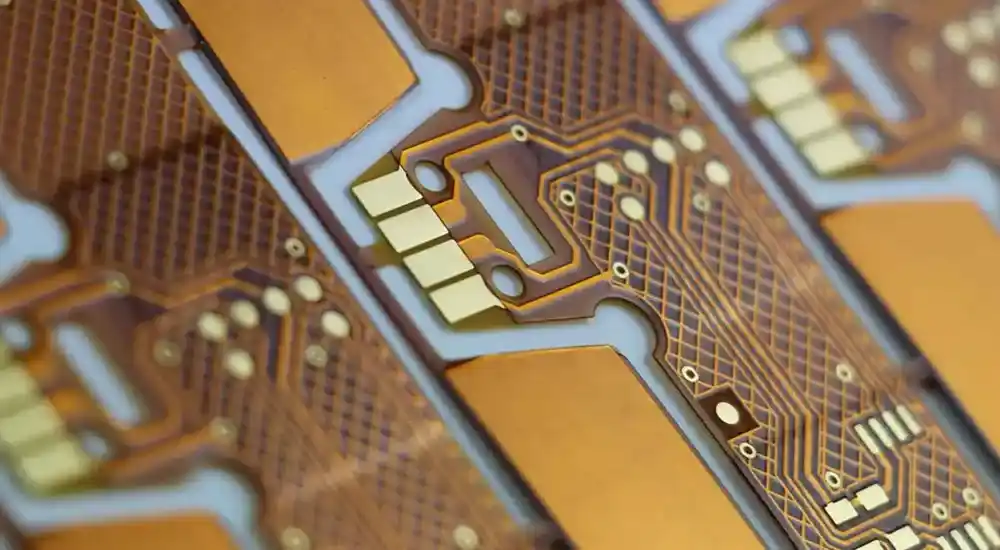
However, flexible PCB material selection involves far more than choosing between PI and LCP. Engineers must balance electrical, thermal, mechanical, and environmental factors. Dielectric properties impact signal integrity; thermal management determines operational stability; mechanical durability affects flex life; and environmental resistance ensures long-term functionality in harsh conditions.
Advanced PI materials, for example, are engineered for high-stress applications. Biphenyl-based formulations can achieve tensile strengths up to 530 MPa and maintain volume resistivity as high as 10¹⁷ Ω·cm. These characteristics form a strong technical foundation for mission-critical systems—from aerospace controls to medical implants—where reliability under extreme operating conditions is non-negotiable.
Polyimide Substrate Materials: Molecular Engineering and Performance Optimization
Fundamental Chemical Structure and Properties
Polyimide represents the predominant flexible PCB material due to its unique molecular architecture consisting of imide linkages that provide exceptional thermal stability and mechanical durability. The linear and stiff cyclic backbone structure of polyimide exhibits significantly lower coefficient of thermal expansion compared to thermoplastic polymers with coiled and flexible chains, resulting in superior dimensional stability across temperature ranges from -269°C to 400°C.
The molecular engineering of modern polyimide formulations addresses specific performance limitations through controlled polymer synthesis. Advanced polyimide substrates maintain glass transition temperatures exceeding 300°C while demonstrating thermal conductivity values suitable for effective heat dissipation in high-power applications. These characteristics enable reliable operation in aerospace avionics systems, automotive engine management modules, and industrial process control applications where thermal cycling represents a primary failure mechanism.
Electrical Performance Characteristics
Polyimide flexible PCB materials deliver superior electrical performance through several key characteristics:
- Dielectric Constant Range: Values typically span 3.3 to 3.5, significantly lower than FR-4 materials (4.5), enabling improved signal integrity in high-speed digital applications through reduced parasitic capacitance and faster signal propagation velocities.
- Loss Tangent Performance: Modern polyimide substrates achieve values between 0.004 to 0.007, representing substantial improvements over conventional materials and becoming increasingly critical at frequencies above 1 GHz where dielectric losses directly impact signal attenuation.
- Volume Resistivity: Maintains 1017 Ω·cm for exceptional insulation performance in high-voltage applications.
- Frequency Stability: Dielectric properties remain consistent across broad frequency ranges, supporting reliable impedance control in high-frequency designs.
Advanced Polyimide Formulations
Modern polyimide development incorporates several specialized formulation approaches to address specific application requirements:
- Low-Flow Polyimides: Built with flow restrictors and specialized resin systems to provide enhanced dimensional stability and reduced material flow during high-temperature processing, essential for applications requiring precise conductor registration and minimal substrate deformation.
- Filled Polyimide Systems: Utilize controlled filler incorporation to enhance specific performance characteristics while maintaining essential flexibility properties, preventing crack propagation and resin fracture during lamination and drilling processes.
- High-Temperature Variants: Engineered for glass transition temperatures exceeding 300°C while maintaining thermal conductivity suitable for effective heat dissipation in high-power applications.
- Low-Moisture Absorption Formulations: Advanced grades achieve moisture absorption rates as low as 0.7% compared to 1.6% in conventional formulations, improving dimensional stability from ±0.04% to ±0.02%.
Liquid Crystal Polymer Technology: Next-Generation High-Frequency Materials
Molecular Structure and Dielectric Performance
Liquid crystal polymers exhibit rigid rod-like molecular chain structures enabling highly oriented molecular arrangements with tight packing density and substantial intermolecular forces. This unique molecular architecture produces exceptional electrical performance characteristics that surpass conventional flexible PCB materials across broad frequency ranges.
LCP materials demonstrate remarkably stable dielectric constants near 3.0 to 3.16 across frequencies extending from DC to 110 GHz, with loss tangent values remaining below 0.002 to 0.0049. These characteristics represent significant improvements over polyimide materials, particularly at millimeter-wave frequencies where conventional materials exhibit substantial performance degradation.
Frequency-Dependent Characteristics
LCP substrates demonstrate exceptional performance across ultra-wide frequency ranges through several key advantages:
- Ultra-Wide Bandwidth Performance: Maintains low loss tangent values up to 1.8 THz with negligible moisture absorption effects, making them ideal for 5G millimeter-wave applications and advanced wireless communication systems.
- Frequency Stability: Functional frequency range extends from 1 kHz to 45 GHz with consistent dielectric performance, enabling circuit designers to implement closer trace spacing without crosstalk concerns.
- Impedance Control: Frequency stability enables consistent impedance control and predictable signal propagation characteristics across ultra-wide bandwidths, supporting higher circuit density and reduced form factors.
- Signal Integrity: Maintained performance characteristics at millimeter-wave frequencies where conventional materials exhibit substantial performance degradation.
Manufacturing and Processing Advantages
LCP materials offer significant manufacturing benefits through their unique thermoplastic properties:
- Adhesiveless Construction: Thermoplastic properties enable direct lamination to copper foil through continuous hot-pressing processes without requiring adhesive layers, eliminating potential reliability issues associated with adhesive degradation.
- Reduced Substrate Thickness: Adhesiveless construction reduces overall substrate thickness while improving electrical performance and maintaining structural integrity.
- Processing Flexibility: Thermoplastic nature provides recyclability advantages and enables secondary processing operations including thermoforming and injection molding for complex three-dimensional circuit configurations.
- Manufacturing Efficiency: Continuous lamination processes improve production throughput while reducing material waste and processing steps.
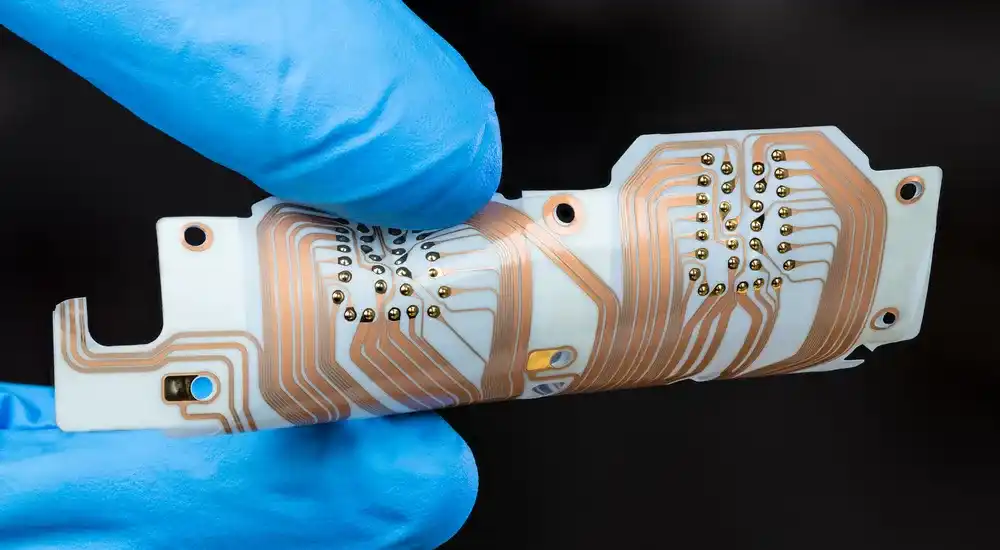
Copper Conductor Systems: Metallurgy and Performance Optimization
Electrodeposited Copper Characteristics
Electrodeposited copper foil provides superior characteristics for high-density flexible PCB applications through controlled manufacturing processes:
- Precision Thickness Control: Typical thickness ranges from 0.5 to 2.0 ounces per square foot (17.5 to 70 micrometers) with uniform distribution across the substrate surface for consistent electrical performance.
- Surface Morphology: Electroplating process produces copper with controlled grain structure and smooth surface finish optimized for photolithographic patterning and high-frequency signal propagation.
- Fine-Pitch Capability: Smooth surface characteristics enable trace width accuracy below 25 micrometers while maintaining consistent impedance characteristics across the substrate.
- High-Frequency Performance: Surface roughness characteristics minimize signal loss and maintain signal integrity in applications above 1 GHz.
Rolled Annealed Copper Properties
Rolled annealed copper foil delivers superior mechanical performance for dynamic applications through specialized metallurgical processing:
- Enhanced Flexibility: Rolling and annealing operations modify copper grain structure, creating elongated grains oriented in the rolling direction that significantly enhance bend-to-failure performance compared to electrodeposited alternatives.
- Fatigue Resistance: Demonstrates exceptional resistance to repeated flexing cycles, with bend radius capabilities approaching 0.5 times the substrate thickness without conductor fracture.
- Dynamic Applications: Essential for applications including printer head assemblies, hard disk drive suspensions, and robotic cable assemblies where repeated flexing occurs during normal operation.
- Mechanical Durability: Superior fatigue resistance enables extended service life in applications with continuous mechanical stress.
Alternative Conductor Technologies
Specialized applications may require conductor materials beyond conventional copper systems to meet specific performance requirements:
- Silver-Filled Conductive Inks: Provide enhanced flexibility while maintaining adequate conductivity for low-current applications, enabling printing processes that eliminate traditional lamination requirements and reduce manufacturing complexity.
- Gold Conductor Systems: Offer superior corrosion resistance and biocompatibility for medical device applications, particularly important for implantable devices requiring long-term reliability in biological environments.
- Aluminum Conductors: Provide significant weight reduction advantages for aerospace applications where mass optimization represents a critical design parameter, while maintaining sufficient electrical performance for power distribution circuits.
- Nickel and Specialized Alloys: Enable operation in extreme temperature environments and chemically aggressive conditions where copper would prove inadequate.
Advanced Adhesive Systems and Bondline Engineering
Acrylic Adhesive Performance
Acrylic-based adhesive systems provide the standard bonding solution for flexible copper-clad laminates, with thickness ranges typically between 12 to 25 micrometers. These adhesives demonstrate excellent adhesion to both copper and polyimide substrates while maintaining flexibility throughout the service temperature range.
The selection of acrylic adhesive formulations must balance competing requirements including bond strength, thermal performance, outgassing characteristics, and electrical properties. Advanced acrylic systems incorporate low-outgassing formulations essential for space applications and medical devices where contamination represents a critical concern.
Adhesiveless Construction Technologies
Adhesiveless laminate construction eliminates the adhesive layer through direct copper deposition or specialized bonding processes, reducing overall thickness while improving electrical performance and environmental resistance. These constructions prove particularly valuable for high-frequency applications where adhesive dielectric properties can degrade signal integrity.
Adhesiveless designs support higher processing temperatures, enabling compatibility with lead-free soldering requirements while providing enhanced dimensional stability and reduced moisture absorption.
Environmental Compliance and Material Sustainability
Halogen-Free Material Systems
Environmental regulations including RoHS and WEEE directives require elimination of brominated flame retardants and other hazardous substances while maintaining equivalent flame resistance performance. Modern halogen-free polyimide formulations achieve necessary fire resistance through phosphorus-based additives and alternative flame retardant technologies.
Halogen-free material systems require comprehensive validation to ensure compatibility throughout the entire material stack, including substrates, adhesives, coverlay films, and protective coatings. These materials enable compliance with international environmental regulations while maintaining performance characteristics required for demanding applications.
Recycling and End-of-Life Considerations
LCP materials offer particular advantages in environmental sustainability due to their thermoplastic nature, enabling recycling and reprocessing capabilities that reduce overall environmental impact. This recyclability addresses growing concerns regarding electronic waste management and supports circular economy principles in electronics manufacturing.
Material Selection Methodology and Design Optimization
Application Requirements Analysis
Optimal flexible PCB material selection requires comprehensive evaluation across multiple critical parameters:
- Thermal Considerations: Operating temperature range assessment, thermal cycling behavior, and heat dissipation requirements determine substrate thermal stability requirements and conductor thermal expansion compatibility.
- Mechanical Performance: Dynamic flexing requirements, bend radius specifications, mechanical stress patterns, and fatigue resistance needs directly influence substrate thickness and conductor type selection.
- Electrical Specifications: Signal integrity requirements, impedance control precision, frequency response characteristics, and dielectric loss limitations establish material dielectric property requirements.
- Environmental Exposure: Chemical compatibility profiles, humidity resistance, ultraviolet radiation exposure, and contamination sensitivity determine protective coating and substrate chemical resistance needs.
- Manufacturing Constraints: Processing temperature limitations, dimensional tolerance requirements, and assembly compatibility establish material processing parameter boundaries.
Performance Optimization Strategies
Material selection significantly impacts controlled impedance characteristics, with higher dielectric constant materials requiring narrower trace widths to achieve target impedance values. This relationship enables designers to optimize conductor geometry and substrate thickness for specific electrical performance requirements.
Cost-performance optimization involves evaluating total ownership costs including material expenses, processing complexity, manufacturing yield, and field reliability performance. High-volume applications may justify premium materials through improved yields and reduced warranty costs, while prototype and low-volume applications often benefit from cost-effective alternatives.
Advanced Design Considerations
High-frequency applications require careful attention to dielectric properties, conductor surface roughness, and substrate thickness variations that impact signal integrity. Materials suitable for high-frequency applications maintain relatively constant dielectric properties across broad frequency ranges, typically from several hundred MHz to multiple GHz.
Mechanical design considerations include bend radius requirements, dynamic flexing profiles, and mechanical stress distribution. These factors determine substrate thickness, conductor type, and reinforcement requirements necessary to achieve specified reliability targets.
Emerging Technologies and Future Developments
Advanced Material Formulations
Fourth-generation polyimide materials under development promise improved adhesion properties and enhanced overall stability while maintaining essential flexibility characteristics. These materials address current limitations in high-density applications and extreme environment operation.
Nanocomposite material systems incorporate controlled nanoparticle additions to enhance specific properties including thermal conductivity, dimensional stability, and electromagnetic interference shielding. These advanced formulations enable performance optimization for specialized applications while maintaining compatibility with standard processing equipment.
Integration with Advanced Manufacturing
Additive manufacturing technologies enable direct printing of conductive traces on flexible substrates, eliminating traditional lamination processes while enabling complex three-dimensional circuit configurations. These approaches support rapid prototyping and low-volume production while reducing material waste and processing steps.
Advanced metallization techniques including direct laser structuring and selective plating enable fine-pitch conductor formation without traditional photolithographic processes. These methods support cost reduction and manufacturing flexibility while maintaining precision required for high-density applications.
Engineering Excellence in Flexible PCB Manufacturing with Haoyue Electronics
The complexity of flexible PCB material selection and the critical nature of material performance in demanding applications require experienced manufacturing partners who combine deep materials expertise with advanced processing capabilities. Haoyue Electronics leverages comprehensive understanding of material science principles and proven manufacturing excellence to deliver optimized solutions for applications spanning consumer electronics to aerospace systems.
Our technical team provides comprehensive material selection support, evaluating application requirements against material capabilities to ensure optimal performance while maintaining manufacturing efficiency and cost effectiveness. With advanced testing capabilities and quality systems certified to international standards, Haoyue Electronics delivers the technical expertise and manufacturing precision required for mission-critical flexible PCB applications.
Whether your project requires standard polyimide constructions for cost-sensitive applications or advanced LCP materials for next-generation high-frequency systems, our engineering team provides the materials expertise and manufacturing capabilities necessary to transform innovative designs into reliable production solutions.